Thermal Cracking of Middle Frames of Aluminum Alloy ADC12 Mobile Phones (Part Two)
2.2
Microstructure analysis of alloys
Figure 3 shows the microstructure of the alloy at the hot crack position observed by an optical microscope. Its metallographic structure consists of primary α-Al, α-Al plus eutectic silicon phases. The part with the light color is the matrix structure, and the dark color eutectic organization. It can be seen from the figure that the hot crack was formed and developed on the grain boundary of the alloy matrix phase. When the crack first formed, the amount of intergranular separation and shrinkage was relatively small, and the eutectic liquid was easily fed. It can be seen from Figure 3a that a large number of gas holes were distributed at the hot crack, which deteriorated the mechanical properties of the alloy, which was consistent with the results observed in the fracture morphology; the grain size distribution of the alloy in Figure 3b and c was not uniform. Coarse dendrites coexisted with fine spherulites, and the presence of a large number of coarse dendrites reduced the thermal cracking resistance of the alloy, indicating that the cooling process was affected by thermodynamics and other factors, resulting in uneven microstructure and great heat stress. Since the coarse dendrites couldn't easily slip and reduce stress like equiaxed and spherical crystals, thermal cracking easily occurred. Figure 3b shows the structure at the tip of the hot crack, in which part of the crack has been filled by eutectic liquid in the formation process, and part of the crack couldn't be filled due to insufficient remaining eutectic liquid, resulting in intermittent cracks. After the hot crack was formed, the temperature of the alloy liquid dropped rapidly and the solidification speed increased due to the narrow solidification interval of the ADC12 alloy; the proportion of the solid phase increased rapidly, resulting in a great decrease in the filling ability of the alloy liquid. The hot crack could no longer be fed. The amount of eutectic liquid was less than that of feeding required for the crack, so that the hot crack couldn't be recovered. Therefore, the hot crack further expanded. Figure 3c shows the structure after the hot crack was expanded, and the crack width was increased, up to 20 μm at the widest part.
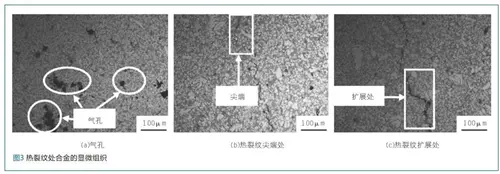
Figure 3 The microstructure of the alloy at the hot crack position
In order to further analyze the microstructure and morphology of the hot crack, the alloy samples were observed by a scanning electron microscope, and the characteristic parts of the hot crack were analyzed by energy spectrum. The results are shown in Figure 4 and Table 3. It can be seen that the component of the white block and needle-like structure in the microstructure contain aluminum, silicon, and iron elements, which were judged to be β (Al9Fe2Si2) brittle phase, and a large number of large-sized big β-AlFeSi phases were on both sides of the crack, and the distribution was disorderly. The feeding channel between dendrites was blocked, making the feeding of the eutectic liquid difficult. At the same time, the gas hole was increased. Because the β-AlFeSi phase has a small gas-solid interfacial energy, the gas holes were easy to nucleate along the β-iron phase and grow. In addition, the coarse and harmful iron phase affects the feeding of the alloy, blocks the channel of liquid feeding, thereby further increasing the hot cracking tendency of the alloy.
Table 3 EDS analysis results of each point in Figure 4
Locations |
Al |
Si |
Fe |
C |
1 |
75.26 |
12.31 |
13.43 |
2.43 |
2 |
73.33 |
13.33 |
13.34 |
|
3 |
74.22 |
12.58 |
13.21 |
|
4 |
56.08 |
19.25 |
3.21 |
21.60 |
2.3
Improvement measures and effects
In view of the thermal cracking in the production process of the ADC12 mobile phone middle frame, the following improvement measures are proposed:
(1) Provide the R angle at the hot joint to reduce the thermal stress in the solidification process.
(2) Reduce the die-cast stub bar and don't use the exhaust plate to prevent the increase of alloy gas content and carbon, oxygen and nitrogen inclusions.
(3) Strictly control the die-cast temperature to prevent liquid aluminum from taking in air, while improving the phase morphology of β-AlFeSi and the high-temperature mechanical properties of the alloy.
(4) Increase the preheating temperature of the mold to 200℃, increasing the preheating temperature of the mold can reduce the cooling rate, slow down the heat loss during the solidification of the alloy, and increase the feeding ability of the alloy liquid, thereby reducing the tendency of hot cracking of the alloy.
(5) Add Al-Ti-B refiner less than and equal to 0.1% before
die casting alloys to improve the microstructure of the alloy and make the α-Al phase distribution uniform. At the same time, low-temperature annealing at temperatures between 250 and 290℃ is adopted and kept for 10 to 16 seconds, thereby reducing the internal stress and improving the strength. After the production process of the die-cast ADC12 aluminum alloy mobile phone middle frame was controlled according to the above measures, thermal cracking didn't happen for the casting, as shown in Figure 5.
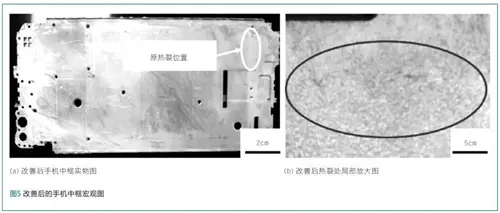
Figure 5 The macrograph of improved mobile phone middle frames
3.
Conclusion
(1) When the ADC12 aluminum alloy mobile phone middle frame is produced by die-cast process, hot cracking occurs at the grain boundary. This is because when the alloy solidifies to the semi-solid stage, the strength limit of the alloy is lower than the thermal stress at the grain boundary; the liquid phase feeding is insufficient at the final stage of solidification.
(2) Through fracture morphology and metallographic observation, it is found that there were a large number of gas holes and carbon and oxygen inclusions on both sides of the hot crack. The scanning electron microscope test results showed that there were many β (Al9Fe2Si2) brittle phases on both sides of the crack, which hinders the feeding channel of the alloy, increases the brittleness of the alloy and deteriorates the mechanical properties of the material.
(3) By optimizing the mold structure, controlling the melting process and improving the die-cast process, the thermal stress of the alloy's solidification process is reduced, and the mechanical properties of the material are improved, thereby eliminating the hot crack of the die-cast ADC12 aluminum alloy mobile phone middle frame.