2.
The test results of aluminum alloy A356
2.1
Influence on the microstructure
Figure 2 shows the microstructure of the samples obtained by the three casting methods, including PMC, LSC and SSC. The alloy structure is mainly primary α-Al and eutectic Si phase. It can be seen from Figure 2a that the α-Al phase is relatively coarse dendrites, and there is no obvious regularity for the orientation. Because the coarse grain size and disordered distribution of the α-Al phase, the eutectic Si phase precipitated at the grain boundary also has obvious segregation agglomeration. It can be seen from Figure 2b that α-Al is significantly smaller than PMC, with rose-like or equiaxed crystals. The organization is denser and the arrangement is more uniform. However, the segregation of intergranular precipitates could not be eliminated. It can be seen from Figure 2c that since the primary α-Al phase is produced in a semi-solid state, it gradually evolves from a rose-like shape to a spherical shape with a relatively round shape during solidification. Casting defects such as gas holes, shrinkage holes and micro-segregation are significantly reduced; the grains are the most round, and the structure is the most uniform.
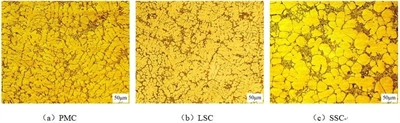
Figure 2 Microstructure of A356 aluminum alloy samples prepared by different casting methods
The results of the statistical analysis of the grain size of the matrix by Image-pro Plus 6.0 software are shown in Figure 3. In the PMC process, the solidification undercooling degree is small, and the α-Al grains are coarse dendrites with an average grain size of 137.807μm. The squeeze casting process greatly improves the heat exchange conditions between the mold and the casting, and under the action of extrusion, the melting point of the alloy increases compared with the traditional casting, which increases the initial undercooling of the alloy melt during solidification. In the LSC process, the latent heat of solidification of the alloy is released quickly, which hinders the diffusion of atoms in the alloy melt, inhibits the growth of the primary α-Al phase, and makes the grain size smaller; the average grain size drops sharply to 43.512μm. As the driving force of solidification, the increase of undercooling reduces the critical nucleation radius, increases the nucleation rate, and increases the number of grains. During semi-solid pulping, the melt produces convection under the stirring action of the drum, causing collisions between grains, inhibiting the formation of coarse dendrites, breaking the dendrite arms, and forming many fine grains. With a decrease in the temperature, these fine grains grow uniformly without obvious orientation; the overall morphology of the α-Al phase is relatively round, and the average grain size is 64.824μm.
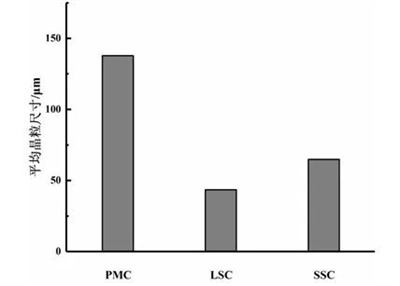
Figure 3 Grain sizes of aluminum alloy A356 α-Al prepared by different casting methods
The Al-Si eutectic is usually regarded as an irregular eutectic, and its growth method is facet growth. The eutectic Si phase was further observed by scanning electron microscopy, as shown in Figure 4. Figure 4a is the electron microscope photo of the eutectic Si phase of the PMC sample. The eutectic Si precipitated on the grain boundary also has obvious segregation and aggregation due to the irregular and uneven arrangement of the α-Al matrix. The eutectic Si phase presents a needle-like or plate-like shape with a large size, which is distributed at the grain boundaries of the matrix, and severely splits the matrix. The eutectic Si grains of the LSC samples were greatly refined and transformed into small flakes and long rods (Figure 4b), but the segregation still existed. After converting the slurry state to a semi-solid state, as shown in Figure 4c, the size of the eutectic Si phase of the SSC sample was significantly reduced. The edge was round and blunt. The overall shape was curved, and showed a worm-like morphology, indicating that in the SSC process, the crystalline Si phase produces a certain degree of spheroidization.
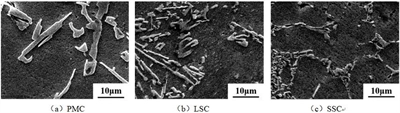
Figure 4 Morphology of eutectic Si phase of aluminum alloy A356 prepared by different forming methods
The
aluminum alloy A356 belongs to the hypoeutectic Al-Si alloy. When solidifying, the primary α-Al phase is first precipitated; the Si phase is precipitated during the eutectic, and is distributed at the grain boundary of the α-Al matrix grains. Therefore, the morphology of the eutectic Si phase is affected by the matrix grains to a certain extent, and the ending of the eutectic reaction also marks the end of the solidification process. Statistics and calculation of eutectic Si equivalent circle diameters, aspect ratio and shape factor are shown in Figure 5. The size distribution of the eutectic Si phase in the PMC sample is relatively dispersed, and there are only a few small-sized grains with a diameter of 2 to 3μm, with an average diameter of 4.40μm and a maximum of 8.32μm; the aspect ratio is 7.92, and the shape factor is 0.34. The size distribution of the eutectic Si phase is also more concentrated than that of the PMC due to the refining effect of the extrusion force on the grains of the LSC sample, and the size is significantly reduced. The average isometric circle diameter decreased to 2.05μm, and the maximum diameter decreased to 4.11μm; the aspect ratio was 6.48, and the shape factor was 0.398. The lower pouring temperature of SSC and the faster cooling rate after filling further reduce the size of eutectic Si and change the morphology. Most of the grains have a radius of less than 2μm. The average diameter is reduced to 1.61μm, and the maximum radius is only 3.5μm. The aspect ratio drops to 3.64 and the shape factor rises to 0.472.
Figure 6 shows the X-ray diffraction patterns of castings with different casting methods. It can be seen that the forming method does not change the phase composition of the alloy. The main phase compositions of the samples cast in the three methods are α-Al and Si phases, and there are strengthening phases (Mg2Si) and Fe-rich phases (Al2Fe3Si4) at the same time. Because the existence of extrusion force accelerates the solidification rate, a small amount of Fe and Mg atoms in the matrix may be dissolved in the matrix to form a solid solution, and it is too late to diffuse and precipitate, which combines to form the second phase (Mg2Si) and Fe-rich phase (Al2Fe3Si4).
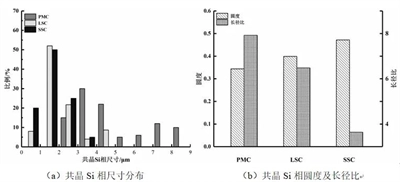
Figure 5 Size distribution and shape changes of aluminum alloy A356 eutectic Si prepared by different casting methods
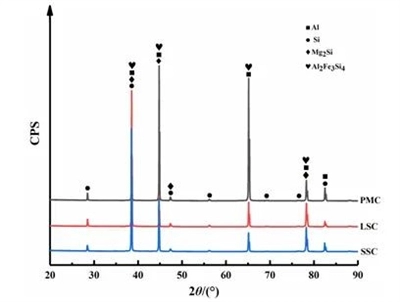
Figure 6 XRD patterns of aluminum alloy A356 prepared by different casting methods
2.2
Influence on thermal conductivity
Figure 7 shows the test results of the thermal conductivity of castings made by different casting methods. It can be seen that the casting method has a significant effect on the thermal conductivity and thermal diffusivity of the alloy. The thermal conductivity of the PMC sample is the lowest; the thermal conductivity of the LSC sample is 2.0% higher than that of the PMC sample, and the thermal conductivity of the SSC sample is the highest, which is 6.7% higher than that of the PMC sample. The specific values are shown in Table 2.
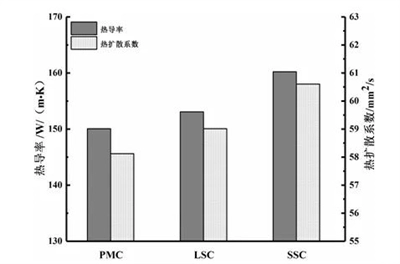
Figure 7 Thermal conductivity of aluminum alloy A356 prepared by different casting methods
Table 2 The morphology eutectic Si phase and thermal conductivity of aluminum alloy A356 prepared by different casting methods