2.2 The corresponding table of the thermal expansion coefficient of die steel material and die casting alloy material at different temperatures
The three commonly used die casting materials are ADC12, A380, and AM50. Their thermal expansion coefficients are shown in Table 1. Take the die-cast aluminum alloy ADC12 with a melting point of 580°C) as an example, and select 8407 as the mold material. The temperature t℃ of the die casting part in the mold decreases from 550°C to 500°C, 450°C and 400°C, and until the room temperature is 20°C; the corresponding thermal expansion coefficients r are 25.3, 24.8, 24.3, 23.8 and so on and is defined as ×10-6 at room temperature. The temperatures of the mold steel 8407 are 450°C, 400°C, 350°C, 300℃ corresponding to the temperature of the die casting part, and the thermal expansion coefficient is 12.89, 12.69, 12.51, 12.33, etc. when the mold temperature is 100℃ lower than the die casting part.
Table 1 The corresponding table of changes of thermal expansion coefficient of die casting and mold temperature changes
The correspondence table for changes of the temperature t of the die casting and mold and changes of the thermal expansion coefficient rx10-6 |
Recommended values |
The temperature of the die casting t ℃ |
20 |
100 |
200 |
300 |
350 |
400 |
450 |
500 |
550 |
370 |
Aluminum alloy ADC12 r |
0 |
21.2 |
21.7 |
22. 8 |
23.4 |
23.8 |
24.3 |
24.8 |
25.3 |
23.6 |
Aluminum alloy A380 r |
|
|
|
23.2 |
23.9 |
24.3 |
25 |
|
|
24.1 |
Magnesium alloy AM50 r |
|
|
|
25.9 |
26.5 |
27 |
27.4 |
|
|
26.7 |
The temperature of the mold t ℃ |
20 |
150 |
200 |
250 |
280 |
300 |
350 |
400 |
450 |
290 |
Mould steel 8407 r |
0 |
11.71 |
11.97 |
12.15 |
12. 27 |
12. 33 |
12. 51 |
12.69 |
12.89 |
12.3 |
①The correspondence table of mold size and die casting part size D and temperature changes: D2=D1[1+r(t2-t1)]
②The shrinkage rate ɑ of molds at room temperature of 20°C equals mold sizes or sizes of die casting parts-1 |
Shrinkage rates of mold design ɑ
|
Sizes of die casting parts (ADC12) |
40 |
40.07 |
40.16 |
40.26 |
40.31 |
40.36 |
40.42 |
40.48 |
40.54 |
|
Sizes of mold (8407) |
40.20 |
40.26 |
40.29 |
40.31 |
40.33 |
40.34 |
40.37 |
40.39 |
40.42 |
Shrinkage rates 0.005 |
Sizes of die casting parts (A380) |
40 |
|
|
40.26 |
40.32 |
40.37 |
40.43 |
|
|
|
Sizes of mold (8407) |
40.24 |
40.30
|
40.33
|
40.35
|
40.37
|
40.38 |
40.41 |
40.43 |
40.46 |
Shrinkage rates 0.006 |
Sizes of die casting parts (AM50) |
40 |
|
|
40.29 |
40.35 |
40.41 |
40.47 |
|
|
|
Sizes of Mold (8407) |
40.28 |
40.34 |
40.37 |
40.39 |
40.41 |
40.42 |
40.45 |
40.47 |
40.50 |
Shrinkage rates 0.007 |
2.3 Shrinkage rates of die casting alloys
It can be seen from Table 1 that when the die casting part is ejected from the mold, the corresponding mold temperature is between 280 and 300℃ when the temperature inside the die casting part is from 350 to 400℃. At this time, the nominal size of ADC12 die casting part and 8407 mold is close. The reasonable recommended values in Table 1 are determined as reference data required for mold design after testing the temperature of molds and castings, as well as statistics on the size and temperature changes of molds in production. In continuous production, the temperature changes of molds and die casting parts tend to be stable. The thermal expansion coefficients of ADC12 when the ejection casting temperature is 370℃ and the mold temperature is 290℃ are 23.6 and 24.1×10-6℃-1 respectively. The shrinkage rate of ADC12 die casting mold design is calculated to be 0.005 according to Table 1, and it can be calculated that A380 and AM50 are 0.006 and 0.007 respectively.
The principle and countermeasures of difficulty in the ejection of die casting parts
When the
die casting part is difficult to be ejected in the mold, the measures of baking the die casting part and then ejecting the die casting part are adopted. When the die casting is difficult to be ejected in the mold, the most commonly used method to deal with the problem on-site is to apply a layer of grease on the joint between the die casting part and the mold, and then bake the die casting part with natural gas to eject the die casting again. The method is simple and effective.
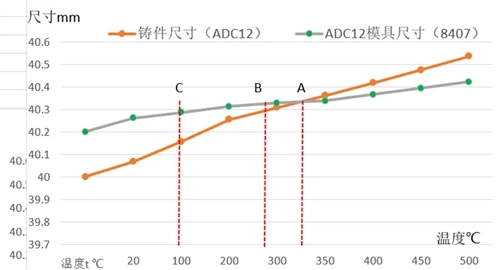
Figure 4 The dimensional changes of the die casting part and the mold at different temperatures when the nominal size is 40mm.
According to Table 1, when the nominal size of the die casting is 40mm (The slope of other dimensions is the same.), the relationship between the mold and the temperature is shown in Figure 4. It can be seen that the size of the die casting part and mold will increase with the increase of temperature, but the slope is different. Point A in Figure 4 is the intersection of the die casting part and mold when they have the same expansion. As the temperature increases, the size of the die casting is bigger than that of the mold.
One of the reasons for the difficulty of ejecting the die casting part is that the production pause causes the temperature of the die casting to drop to the C zone, and the shrinkage of the die casting part makes the size smaller than that of the mold, resulting in greater packing force. The baking method is used to increase the temperature of the die casting part, and the thermal expansion is increased to the reasonable B zone, even A zone, which is bigger than the size of the mold, so that the packing force is reduced. However, the temperature rise should not be too much. Otherwise, the die casting part will be penetrated due to the reduced strength of the part. In this process, you can adopt the method of baking while trying to eject the part. This method is fast, simple and effective. Otherwise, the part needs to be removed from the mold by an operator, which is time-consuming and labor-intensive.
4.
Conclusion
The thermal expansion slope of die casting parts and die steel is different, and the intersection point is the point where the thermal expansion of the two is equal. When the die casting enterprise encounters difficulty in ejecting the die casting part in the production, the method of baking the die casting part is adopted to make the thermal expansion of the die casting part near the intersection of the slope, which can greatly reduce the packing force of the die casting part and eject the die casting part smoothly.