The packing force of die castings changes dynamically from the beginning of the cooling of the aluminum alloy in the mold to the ejection of
die castings. The mold materials and alloy materials have different thermal expansion coefficients corresponding to temperature changes, and different shrinkage rates are selected according to different die casting alloys during mold design. Fail to eject the die casting caused by temperature changes in the production of the die casting factory can be solved by temperature adjustment.
During the solidification of the die casting alloy, the shrinkage of the die casting produces a packing force on the mold, and the mold material also shrinks with the change of the temperature. The coordinated change of the die casting and mold causes a dynamic change in the packing force. The die casting has a certain temperature after being ejected from the mold and will shrink when it is cooled to room temperature. The design manual of the mold recommends that the shrinkage of die casting should be between 0.4% and 0.7%. This dynamic change makes it difficult for mold designers to choose shrinkage rates. In fact, the packing force of the die casting is closely related to the draft angle, finish of the mold, layout of the ejector pin, concentration of the release agent, mold temperature, die casting temperature, etc. The shrinkage rate and thermal expansion coefficient of molds and die castings are only analyzed and parameters for selecting mold shrinkage rates during mold design are provided in this subject. An effective countermeasure is provided for die casting manufacturers when they encounter difficulties in ejecting die castings caused by temperature changes.
1. Coefficient of thermal expansion of metal materials
The thermal expansion coefficient involved in the die casting process is mainly die steel and die casting materials.
1.1.
The thermal expansion coefficient of die steel
The commonly used die casting mold materials are 8407, DIEVAR, H13, SKD61, etc., which all belong to the same type of metal materials. For aluminum alloy die casting, the mold temperature is between 75 and 425 ℃ after the mold is preheated during normal production (Figure 1). Different die casting companies have different mold temperatures, and companies can make statistical confirmation based on huge amounts of data to select the corresponding thermal expansion coefficient of the mold according to the mold temperature.
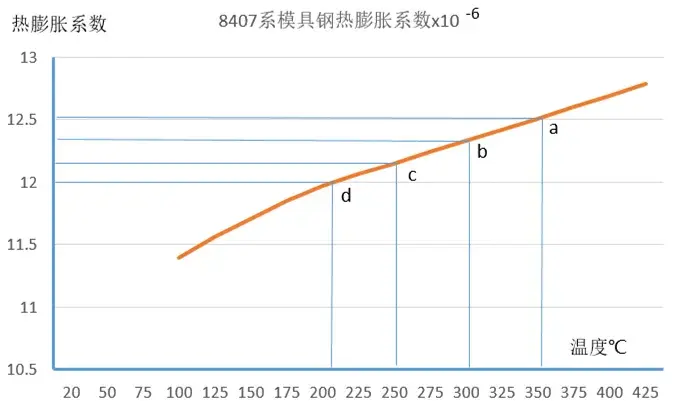
Figure 1 The relationship between the temperature of the mold material and the coefficient of thermal expansion
1.2
The thermal expansion coefficient of aluminum alloys and magnesium alloys
The thermal expansion coefficient of die-cast aluminum alloy and magnesium alloy is mainly related to the Si content. The higher the Si content is at the same temperature, the smaller the thermal expansion coefficient will become. Figure 2 shows the thermal expansion coefficients of three commonly used die casting materials, that is ADC12, A380, and AM50. The vertical line is the median value of the material composition requirements. Die casting manufacturers can know the thermal expansion coefficient according to their company's common Si content.
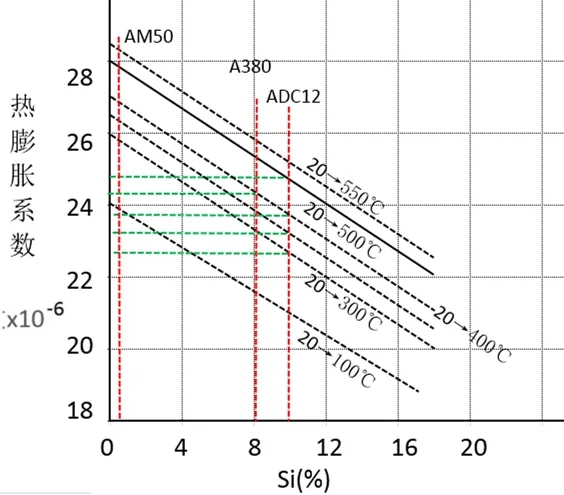
Figure 2 The thermal expansion coefficient of die-cast alloys
2.
Selection of shrinkage rates of die casting molds
When selecting the shrinkage rate of the design of die casting molds, it is necessary to comprehensively select the mold material, type of aluminum alloy, and temperature of the mold in the die casting process.
2.1
The temperature of die casting parts and molds
The shrinkage rate used in mold design is defined as the change in the size of the die casting that begins to cool to room temperature at the moment when the die is ejected from the mold. The measured die-cast aluminum alloy is ADC12. The maximum temperature of the Ar1 area of the mold measured by the thermal imager is 289.5 ℃. The mold still rapidly cools when the die casting is ejected. The measured external temperature of the die casting is 350℃, and the internal temperature is about 400℃. This thermal imager has a delay in measuring the temperature. The temperature is about 50℃ lower than the actual temperature. See Figure 3.
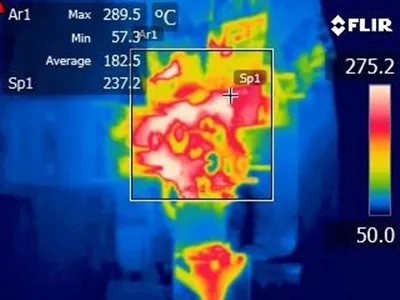
Figure 3 Thermal imaging temperature of the mold