Casting aluminum alloys are widely used in automobile manufacturing and aviation industry due to their excellent casting properties, good corrosion resistance, high specific strength and low production costs. A356 aluminum alloy is a commonly used casting Al-Si alloy, because of its good fluidity, good air tightness, low shrinkage and low thermal tendency, which is usually used to manufacture automobile engine cylinder heads, slider components and wheel hubs and other castings with complex structure. With the development of the automobile industry, the expansion of its application range has put forward higher requirements on the mechanical properties and heat dissipation capacity of the parts. The tensile strength of the die-cast A356 alloy is about 180MPa, the elongation about 5.0%, and the thermal conductivity at room temperature about 150.7 W/(m∙K). The main factors affecting the mechanical properties of casting
aluminum alloys include the type, size and morphology of phases in the alloy, and the nature, quantity and distribution of casting defects. The process of squeeze casting has a refining effect on the grains and increases the density of the structure due to the action of pressure, thereby improving the mechanical properties of the casting. The tensile strength of liquid extrusion castings can reach 208.975MPa, and the elongation can reach 8.58%.
1.
Test materials and methods of A356 aluminum alloys
1.1
Test materials
The test material adopts commercial A356 aluminum alloy, and its composition is shown in Table 1.
Table 1 The chemical composition of the A356 aluminum alloy (%)
1.2
Test methods and equipment
Three different casting methods including PMC, LSC and SSC were used in the experiment. Among them, PMC uses SG-7.5-10 pit crucible resistance furnace to remelt commercial A356 aluminum alloys. When the temperature rises to 720°C, C2Cl6 with a mass fraction of 1% is added for refining (degassing and slag removal) and then left to stand. Pour the liquid into a mold preheated at a temperature of 250℃ to obtain castings. A 600T horizontal squeeze casting machine was used for squeeze casting. The injection force was 784kN, the specific pressure 101MPa, and the pressure maintaining 15 seconds. The aluminum alloy liquid is poured into the barrel of the squeeze casting machine preheated at a temperature of 250°C after being refined and slags being removed; the alloy is pushed into the mold preheated at a temperature of 250°C for extrusion. In SSC, the melted A356 aluminum alloy melt is poured into a drum-type semi-solid slurry machine for pulping with the outlet temperature of 590°C, and then injected into the extruder barrel for extrusion. The size of the formed part is 160 mm × 170 mm × 8 mm.
After the samples made by different casting methods were ground and polished by rough grinding and fine grinding, they were corroded with 0.5% HF solution for 20 seconds. The microstructures of the three castings were observed under a metallographic microscope (4XG-MS). The eutectic Si phase and tensile fracture were observed by scanning electron microscope (QUANTAFG-450). An X-ray diffractometer (D/max-2400) was used for phase analysis; 2θ was 20° to 90°, and the lattice constant was analyzed by Jade5.0 software.
The thermal diffusivity was measured by the LFA457 laser thermal conductivity analyzer; the test temperature was 25°C, and the sample size was φ12.7 mm×5 mm; the specific heat capacity was measured by the STA449C synchronous thermal analyzer and the thermal conductivity was calculated as follows:
λ=α•ρ•c (1)
In the formula, α is thermal diffusivity (m㎡/s); ρ is density (g/cm3); c is specific heat capacity, J/(g•K).
Use a wire cutting machine to cut the tensile sample (Figure 1). Use the WDW-100D electronic universal material testing machine to conduct a tensile test, and record the tensile strength and elongation of the sample. The alloy hardness was tested by the HB-3000B Brinell hardness tester.
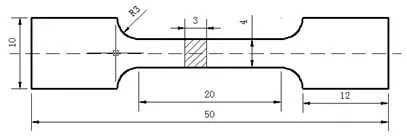
Figure 1 The schematic diagram of the tensile specimen