Abstract: The slag inclusions in the gate of
aluminum alloy die castings are mostly in the form of shrinkage cavities, oil stains and chilled hard layers. The main causes of slag inclusion are high temperature of the die casting die, excessive punch oil and high slag content in Al liquid. To solve the slag inclusion of shrinkage cavity, mainly start by reducing the temperature of the die casting mold.
Preventive measures for oxidation slag inclusion of
aluminum alloy die castings are as the following:
Strictly control the smelting process of aluminum alloy die castings; quickly smelt; reduce oxidation and remove the slag thoroughly. The Al-Mg alloy must be smelted under the covering agent. The furnace and tools should be cleaned and free of oxides, and preheating should be performed. The paint should be dried for use after coating. The designed pouring system must have stable flow, buffering and slag skimming capabilities. The inclined pouring system is adopted, and the liquid flow is stable. No secondary oxidation occurs. The selected paint should have good adhesion and will not peel off during the pouring process, entering the aluminum alloy die casting to form slag inclusions.
Aluminum alloy die castings are generally made from ADC11 or ADC12. The chemical composition of ADC11 is as the following:
The chemical composition of ADC11 aluminum alloy %
|
Si |
Fe |
Cu |
Mn |
Mg |
Zn |
Ni |
Sn |
Al |
Reference values |
7.5 to 12.0 |
≤1.3 |
1.5 to 4.0 |
≤0.5 |
≤0.3 |
≤1.0 |
≤0.5 |
≤0.3 |
The rest |
Measured values |
10.75 |
0.78 |
1.61 |
0.18 |
0.14 |
0.47 |
0.06 |
0.03 |
The rest |
Slag inclusion forms and formation mechanism
Through analysis of the scrap parts of aluminum alloy die castings, there are three main forms of slag inclusions in the gate: shrinkage cavities, oil stains and chilled hard layers, among which slag inclusions of oil stain forms account for more than 60% of the total slag inclusions. The chilled hard layer accounts for about 35% of the total slag inclusions and the shrinkage cavity type 5%.
Reasons for oxidation slag inclusions of aluminum alloy die castings
1. The furnace burden is not clean, and the amount of recycled furnace burden is too much.
2. The gating system is not designed well.
3. The slag in the alloy liquid is not cleaned well.
4. Improper pouring brings slag inclusions.
5. There is not enough standing time after refining and deterioration treatment.
(1) The slag inclusion part at the gate (2) The enlarged view for the slag inclusion part
1. Shrinkage cavity types of defects
After knocking the runner cake material of aluminum alloy die casting parts, holes with irregular shapes, relatively clean insides and rough outer surfaces being similar to shrinkage cavities appear at the gate. The pouring gate surface of shrinkage cavity type slag inclusion of aluminum alloy die castings has dents, and the appearance is still not smooth after polishing and coating. The reason is that the inner gate temperature is relatively high. The measured maximum mold temperature is 380°C. The last solidified part causes the Al liquid to be too late to feed, resulting in shrinkage cavities.
2. Oil stain types of defects
Lubricating oil needs to be added to the punch for every die casting cycle. The punch oil is not completely burned after the Al liquid is poured, which is wrapped in the Al liquid to form impurities and fill the cavity together. Because the temperature of the Al liquid wrapped with punch oil is low, it will solidify earlier and flow at a slow speed. Therefore, it stays at the end of the product at the end of filling. In addition, the cross-sectional area of the inner gate is small and the flow resistance is great. This part of the Al liquid impurity that is wrapped with punch oil and solidified in advance is not easy to pass, resulting in stagnating near the inner gate. After knocking the cake material, a black hole appears at the inner gate. The inner wall is rough, and the surface has obvious oil stains. Such impurities are found after checking the pouring gate and cake material.
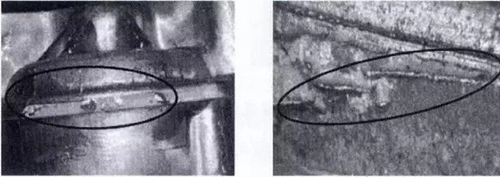
1. The slag inclusion at the gate 2. The enlarged view for the slag inclusion part
3. Chilled hard layer types of defects
The chilled hard layer refers to the shell formed by the rapid condensation of the Al liquid injected into the barrel and the low temperature surface of the barrel (the spectrometer checks chemical composition of the chilled hard layer and no abnormalities are found, all within the standard allowable range). The shell is filled into the cavity along with Al liquid at a high speed. The density of the solid chilled hard layer is 2.7g/cm², which is greater than that of the liquid Al. The liquid Al has a density of 2.45g/cm². During the low speed operation stage of the punch, the chilled hard layer slowly gathers at the end of the Al liquid. When the punch is running at high speeds, parts of the chilled hard layer will be cased in the cavity and form defects. They will become the chilled hard layer remaining in the gate finally. The chilled hard layer mostly has the shape of thin slices, and is shiny and hard. Moreover, there are many gaps between the chilled hard layer and surrounding base material, which not only affects the appearance, but also reduces strength of aluminum alloy die castings.
Summarize shortcomings of existing production conditions and the relevance to slag inclusion, so as to formulate corresponding improvement measures to ensure the appropriate mold temperature, correct the wrong punch lubricant supply method, realize the standardization of aluminum alloy melting and verify the effect, so that the slag inclusion problem can be effectively controlled.