With the ongoing advancements in die-casting technology, the improvement of large-scale die-casting equipment, and the growing demand for lightweight production, high-strength and tough
die-cast aluminum alloys are widely used in fields such as automotive, aerospace, and electronic equipment. Common types include Al-Si, Al-Mg, and Al-Si-Mg alloys. Among these, Al-Si alloys are widely used in automotive parts production due to their excellent casting properties, good fluidity and filling ability, easy demolding, and low density.
Due to rapid changes in the automotive industry, energy conservation and emission reduction have raised higher requirements for automobile lightweighting. The use of large high-pressure cast structural parts to achieve body integration has become an industry trend. For large, complex-shaped die-cast aluminum alloy body structural parts, heat treatment poses significant challenges. During the die-casting process, the melt fills the mold cavity at high pressure and speed, leaving little time for gas to escape, leading to defects such as internal gas holes. High-temperature solution treatment often causes surface blistering of the workpiece, and quenching thermal stress can result in severe distortion or even cracking. Therefore, the demand for die-casting alloys that meet user requirements without heat treatment is growing. Ultra-vacuum die-casting, semi-solid thixoforming, or rheo-die-casting technologies can be used to produce high-strength and tough die-cast aluminum alloys without heat treatment, but the equipment is complex and process control is challenging. Shusen Wu and others developed a high-strength and tough aluminum-silicon AlSi10 alloy for die-casting. After low-temperature aging treatment at 150 ℃ for 6 hours, its tensile strength and yield strength reached 333MPa and 237MPa, respectively, with an elongation of 5.4%, ensuring the alloy’s comprehensive mechanical properties. XUE Z Z and others performed only an aging treatment at 200 ℃ for 1.5 hours on high-vacuum die-cast A356 (AlSi8) aluminum alloy, achieving a tensile strength of 286.0MPa, a yield strength of 193.8MPa, and an elongation of 7.86%.
It is evident that the preparation of Al-Si alloy samples by high-vacuum die casting still requires heat treatment to enhance their mechanical properties; in the ordinary die-casting process, achieving the expected performance without heat treatment is even more challenging. This project conducts low-temperature aging heat treatment research on ordinary die-cast samples of a new AlSi7CuMnMg alloy, an improvement on A356 from a specific company, to avoid bubbles and deformation caused by high-temperature solution treatment and quenching. While ensuring the surface quality and geometric accuracy of the alloy, the study investigates the impact of different aging treatment systems on the microstructure and mechanical properties of the alloy samples. Through exploration, a feasible low-temperature heat treatment process is developed to serve as a reference for the development and application of related alloys.
The AlSi7CuMnMg alloy is formed using a horizontal die-casting machine, with an effective injection length of 310 mm, a punch diameter of 50 mm, an injection time of 5 seconds, a cooling time of 1 second, and an injection speed of 55 mm/s. The die-cast sample is shown in Figure 1, and the chemical composition of the AlSi7CuMnMg aluminum-silicon alloy is shown in Table 1. After solution quenching treatment, noticeable blistering and deformation appear on the surface of the sample. These defects can be avoided by performing only low-temperature aging heat treatment. For this alloy, only a low-temperature aging heat treatment orthogonal test is conducted to explore the influence of aging time and temperature on the microstructure and mechanical properties of the alloy (Table 2).
Table 1 Main element content of AlSi7CuMnMg alloy
Element |
Content (%) |
Si |
6.84 |
Cu |
0.623 |
Mn |
0.408 |
Mg |
0.285 |
Fe |
0.14 |
V |
0.108 |
Sr |
0.0286 |
Al |
Remainder |
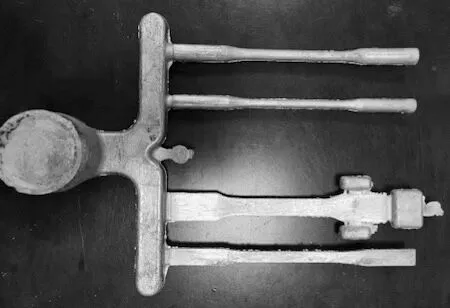
Figure 1 Die-casting sample
Table 2 Aging treatment scheme
Aging temperature/°C |
Aging time/h |
150, 160, 170, 180 and 190 |
6 |
170 |
2, 4, 6, 8 and 10 |
The mechanical properties of samples subjected to different aging treatments were tested using an electronic universal testing machine. The tensile speed was set to 1 mm/min. Three parallel samples were prepared for each test, and the average value was recorded. The 10 mm cylindrical sample was cut using CNC wire cutting, coarsely ground with 400, 800, and 1200-grit water-abrasive sandpaper, and then finely ground with 400, 800, and 1200-grit metallographic sandpaper. It was then polished with abrasive paste, with a selected particle size of 0.5 µm, corroded with Keller's reagent (2 mL HF + 3 mL HCl + 5 mL HNO₃ + 190 mL H₂O) for 5 seconds, rinsed with water, cleaned with alcohol, and blown dry. The microstructure was then observed using a Leica DM IRM optical microscope (OM). The microstructure and tensile fracture morphology of the alloy were observed using a JEOL JXA-8100 scanning electron microscope (SEM), and the alloy composition was analyzed using the OXFORD-7412 energy dispersive spectrometer (EDS) equipped with it. Phase analysis of the samples was performed using an X-ray diffractometer in combination with Jade 6.0 software.