When it comes to the leader of the new energy automobile industry, there is none like Tesla, because Tesla's new energy vehicles have a leading share in the global market. The proposed "one-piece die-cast" process leads the future development trend of lightweight structural parts.
Recently, Tesla's CEO Musk said at the Open Day event in the Berlin New Factory that the mass production of Model Y and battery packs in the Berlin Super Factory would be 5,000 sets per week, and reach 10,000 sets per week in the future. The manufacturing would start in November and the products could be delivered to customers in December.
According to a person in charge of Tesla, it is hoped that the factory can produce 520,000 cars per year, an average of 10,000 cars per week, which means that a new Tesla car will be manufactured in the factory every 45 seconds.
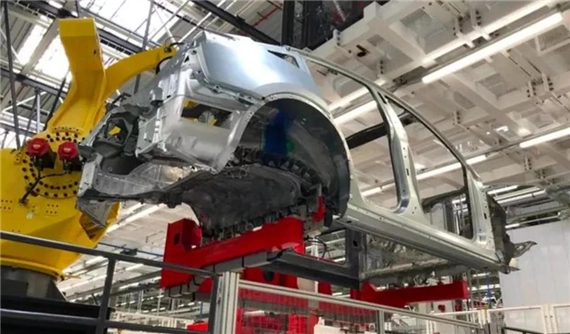
Mass production of one-piece super-large structural parts
A year ago, Tesla's CEO Musk praised a large die-cast machine of 410 tons on Twitter, which was equivalent to five space shuttles. He said that this super-large die casting machine would bring a revolution in the design and production of the body, realizing products with lighter weights, small sizes, better NVH, higher precision, lower capital expenditure and unit costs.
On the Battery Day last year, Musk said that Model Y would use the integrated die-cast rear floor technology, which would greatly reduce the weight of Model Y's lower body assembly and manufacturing costs by 40%. Musk's view became one of the most googled topics for a while, which not only became the hot topic among die-cast industry practitioners, experts and scholars, but also started an industrial wave in the die-cast industry in China.
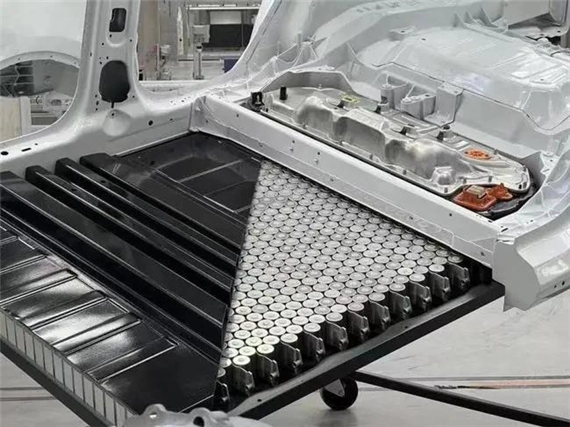
Integrated chassis battery packs
Recently, Tesla's Berlin factory is opened to the public for the first time, and the Berlin factory showed the integrated chassis battery pack for the first time. The new battery pack will be firstly installed on the Model Y. It is reported that the new battery pack would use the third-generation 4680 cylindrical cells released on Battery Day last year. This cell which was released on Battery Day last year was Tesla's third-generation cylindrical cell after 1865 and 2170. "There is no need to put another box in the box," said Musk, when talking about this new one-piece chassis battery pack. The new battery pack no longer has battery modules, but is directly covered with 4680 cells, which greatly reduces the middleware in the battery pack and improves the volume utilization of the battery pack.
In addition, Tesla's Berlin factory also exhibited an integrated die-cast Model Y front body, a Berlin factory Idra's 6000T die casting machine, a Model Y die-cast front body and body assembly, an integrated battery pack and an integrated die-casting machine molds that can mass-produce large-scale structural parts by integrated die casting processes.
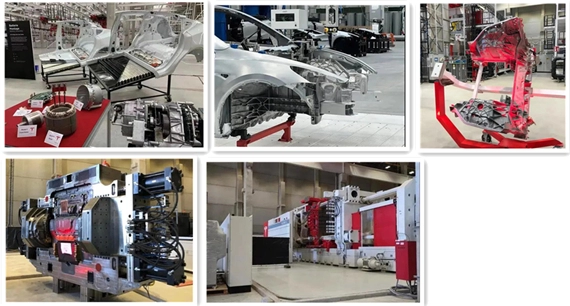
Part of the MODEL Y structural parts and die casting machine mold equipment displayed on the open day of the Berlin factory
At present, Tesla adopts a method of combining battery cells into modules like most automakers, and modules are combined to form a battery pack. The battery pack is then installed on the vehicle platform. The integrated chassis battery pack will no longer use modules. Instead, the entire battery pack will be built as the structural platform of the vehicle, and the entire platform will be fixed as a whole by only the batteries. Coupled with Tesla's expertise in one-piece die casting, Tesla can connect the one-piece front and rear body bases to this structural battery pack. This new design reduces the number of parts and the total weight of the battery pack, allowing Tesla to increase efficiency and ultimately increase the cruising ability of the model.
According to the above public information, it is believed that with the help of multiple mature production processes such as intelligent manufacturing, integrated die casting molding, and integrated chassis battery packs, it is possible to produce a new car at an average of 45 seconds. After all, science and technology are the primary productive forces.
Does Model Y show Tesla's top technology?
A long time ago, Tesla launched the production project of the Model Y and made several major improvements in production, including the introduction of a large die-cast machine, which could make most frames of the Model Y form a large part.
For this reason, Tesla also announced a patent application, indicating that Tesla is using a new casting machine to produce Model Y. The patent is titled "Multi-directional body integral molding casting machine for automobile frames and related casting methods".
Tesla described the current problems in the die-cast process of vehicles. Generally speaking, different die casting machines are required for die casting different parts of the frame in the manufacturing and die casting processes of frames. For example, a single die casting machine in a factory is used for die casting individual frame components. Then, the workers or robot systems will assemble or fix the
die-cast components by each die casting machine by welding or other ways to form a frame, for example, an integrated frame. Compared with other manufacturing processes, the die casting process usually costs much. Therefore, it is necessary to improve the die casting machine and related die casting methods. Tesla proposed a system that allows several protruding dies to meet in a center.
Tesla believes that this design can reduce production time, operating costs, production costs, factory floor space, factory operating costs, tool costs, and the number of equipment.
In addition, Tesla even stated that this mold can reduce the number of casting machines used for producing frames and produce a complete or partially complete frame by itself. One-piece die casting parts have complex structure, high manufacturing costs, and long preparation periods, and are more suitable for mass production of approved products. Excellent sales results must be created or more models on the same platform must be developed for Model Y with integrated rear floors and Cybertruck with integrated lower bodies to take advantage of the supply chain advantages of integrated parts and effectively share the manufacturing cost of die casting parts.