The mold coating process is to coat the surface of the mold with a layer of high-impact alloy. Using cold welding, the super hard alloy is quickly coated on the surface of the mold in a short time and penetrates the structure of the mold. After coating, the wear resistance, corrosion resistance, impact resistance, mold release and heat resistance of the coated mold can be increased.
1.1
Microstructure of die-casting mold after coating
The thickness of the covered part increases. To increase the coating effect within the tolerance range required by the casting drawings, the mold coating area can be covered with multiple layers, and the thickness of the coating layer can be controlled at 0.01 to 0.1 mm, which can be adjusted freely according to the actual situation.
Figure 1 The metallographic microstructure of the coating layer
1.2
Coating materials and physical properties of molds
The coating material for the mold is WTC-90. A small amount of titanium is added based on WC to reduce its brittleness. In the mold coating process, there is no need to heat the coated mold, and the coating at room temperature will not cause thermal deformation. There will be no stress concentration in the coated area, so it will not cause cracks in the coated part due to stress, and the tungsten carbide coating has excellent ultra-high hardness and is outstanding in terms of scouring resistance.
2.
Influence of the mold coating process on casting quality
The mold design is affected by the casting structure. In the actual production process, limited by the design, the process window is relatively narrow, and casting defects exist at the same time. In principle, the process setting must first ensure the internal quality of the casting, but the appearance of the casting often does not meet the customer's requirements. With the scouring of the gate, the gate part of the casting is cracked; the cooling water cannot be installed at the sharp corner of the mold, resulting in excessive temperature, burning and sticking aluminum; there are many grooves in the mold, and the resistance encountered in the filling process of aluminum liquid is relatively great. Flow marks occur on the surface of the casting. After the shot blasting of the casting, peeling happens on the appearance of the casting. Given these problems, the introduction of coatings in the early design and later production of the mold can effectively solve the above defects.
2.1
Improvement in the mold coating process on cracks of castings
Figure 2 shows the design of the pouring system of the oil cooler cover and the position of the drawing mold.
Figure 2 Schematic diagram of the pouring system of the oil cooler cover and the position of the drawing mold
The position of the drawing mold is located at the end of the ingate. Through repeated verification of the die casting process, it has been found that reducing the speed can reduce the scouring of the part of the die, but the position of the mold cannot be eliminated, leading to the poor appearance of the product. The depth of the drawing mold is more than 0.5 mm (Figure 3), and cracks appear in severe cases, especially invisible cracks.
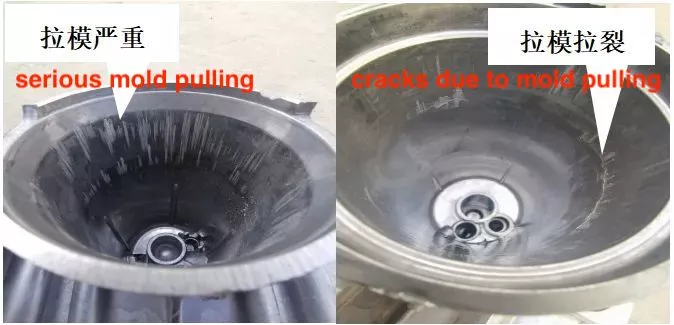
Figure 3 Appearance defects of casting molds
The mold is coated with 2 layers of coatings, and the thickness of the coating is 0.05 mm. After verification, the defects of the drawing die are solved, and the adjustment of the die-cast process, especially the requirement for speed is flexible. Figure 4 shows the comparison of castings before and after shot blasting after coating, which fully meets the customer's requirements.
Figure 4 A comparison before and after shot blasting of coated castings
2.2
Improvement in casting sintering and aluminum adhesion by the mold coating process
When liquid aluminum hits the cavity or core at high speeds, the temperature of the impacted part of the mold rises, so a chilling layer cannot be formed, and the liquid aluminum corrosion of the mold will occur. There will be a coarse layer on the blank. (Figure 5)
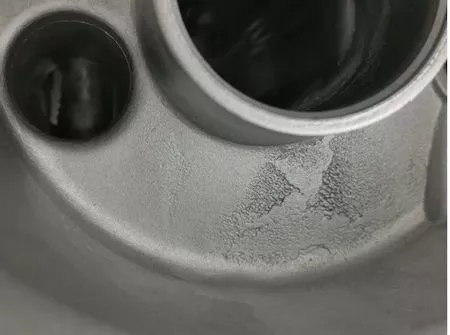
Figure 5 Partial sintering of castings
Generally, in the die-cast process, cooling water is set for the sintering part to reduce the partial mold temperature, which can reduce sintering. However, often affected by the mold and product structure, cooling water cannot be set in some positions. If the amount of release agent spray is increased, the production cycle will be affected. It has been verified that coating the partially sintered part can effectively solve the partial sintering. (Figure 6)
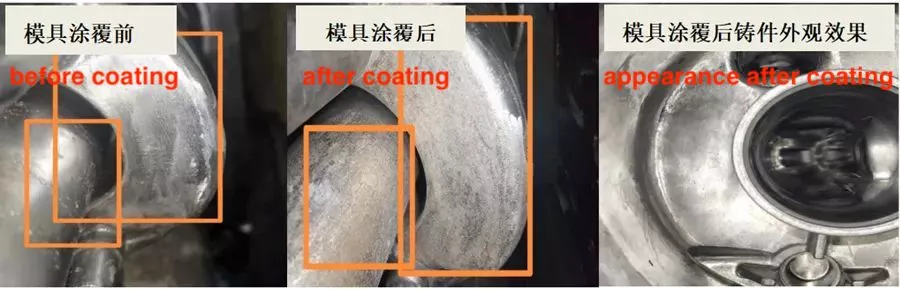
Figure 6 A comparison before and after coating the mold
2.3
Improvement in die-cast mold coating process on shot blasting of castings
After the shot peening, a layer of thin skin will appear on the surface of the casting, and even fall off. It can be easily removed by fingers, and its size, area and position are not fixed. This is known as post-blasting peeling. (Figure 7)
Figure 7 Peeling after shot blasting
The main reason for the peeling of castings is that some castings are specially designed. There are many grooves, and the molten aluminum fluctuates greatly in the filling process. When filling the mold at high speed, the molten aluminum flows to the place where the main flow cannot be filled, and the molten metal splashes. The temperature drops fast, and it has solidified before the mainstream reaches and the supercharging begins. Therefore, cold scar flow marks or pitted surfaces are formed on the surface of the casting, and cold scar flow marks and pitted surfaces are the main reasons for shot blasting (Figure 8).
Figure 8 Schematic diagram of water-cooled shell pouring system and casting structure
During the flow of molten aluminum in the cavity, if the mold is coated at the position where the casting is prone to cold scars and pits, the surface of the mold will be rough and uneven due to the smooth surface of the mold. The flow direction of the aluminum liquid in the cavity will be dispersed, and form a layer of air film between the grooves, improving the fluidity of the aluminum liquid at this position, and avoiding or reducing the generation of cold scar flow marks or pits. It has been verified that the coating of the mold can effectively solve the cold scars, flow marks and pits on the surface of the casting, and there is no peeling after shot blasting (Figure 9).
Figure 9 Shot blasting appearance of castings after mold coatings