Aluminum alloy die casting is the casting process that injecting the high temperature molten aluminum alloy liquid into die cavity with high pressure and high speed for moulding. Features of this casting method are product precise forming and high production efficiency. However, the conventional
die casting process is defective. Because the gas in the mold cavity cannot be eliminated effectively, the gas in the mold cavity cannot be eliminated effectively, and the inner parts of the casting can be left to form the defects of the pores, to make the mechanical property of the casting poor. In order to solve this problem, people use the method of vaccum pumping, that is, the gas in the cavity of the die casting can form a certain vacuum or negative pressure state, thereby reducing the inner hole defect of the casting.
For a long time, in order to widen the application range of the die casting and improve the mechanical properties of the die casting parts, some new methods such as the laminar flow filling method (ultra low speed die casting method), die filling method and vacuum die casting method were studied. The main purpose of the method lies in reducing the volume of gas in the filling process of liquid metal, so as to improve the mechanical properties of the castings. Due to the low production efficiency of the laminar filling method, the complicated operation process, the process parameters are not easy to control. Two methods are seldom applied in actual production. The vacuum die casting rule is that the gas in the cavity is drawn out, and the metal liquid is filled in the vacuum state, so the gas is less, and the mechanical properties of the casting are improved. And vacuum die casting is the same as ordinary die casting method, the operation is convenient and does not reduce the production efficiency. Therefore, since the vacuum die casting method come into application, it has shown great vitality, with the development of related technology, it will have wider and wider application.
1. Test
The material used in the test is ADCI2 aluminum alloy, and the standard rod tensile test specimen with a diameter of 6mm is prepared by the KN type horizontal cold chamber die casting machine with the locking force of 1800 J1118F and the DIEVS60-SUM9 vacuum device. Chemical compositions of the material used in the test is shown in table1.

Common die casting samples and vacuum die casting samples are divided into two parts, T6 heat treatment is applied to one part of each sample, the other part of each sample doesn't be disposed. Then, test their mechanical properties. Tensile tests were carried out in the CSS-1120 type electronic universal testing machine, hardness testing in HB-3000 Brinell hardness, head diameter of 5mm, the load value is 2.452KN, maintain the load time of 30s, the environment temperature is 18 ℃.
In this test, the pouring temperature of the liquid aluminum alloy is 660, pressure is 11MPa, low speed is 0.2m/s, high speed is 5m/s.
2. The result and analysis of the test
2.1. Appearance quality
Figure 1 and Figure 2 are vacuum die casting samples and common die casting samples after heat treatment. As can be seen from the diagram, the surface of the vacuum die casting sample is very little. In contrast, the surface of the common die cast specimen has a lot of bubbles, which is formed by the high temperature expansion of the internal gas of the casting.
Fig.3 section photos of two specimens after tensile strength test. The left side of the figure is the section of the common die casting sample, the right side is the section of the vacuum die casting specimen. It can be seen from the figure that the section of the common die casting specimen is rough, the color is dark, the section of the vacuum die casting sample is close, and the color is more close to the color of the aluminum alloy. After Measure the diameter of the same parts of the sample, compared with the heat treatment, it is found that the diameter of the ordinary die casting samples increased by more than 0,1mm, while the vacuum die casting samples have almost no change.
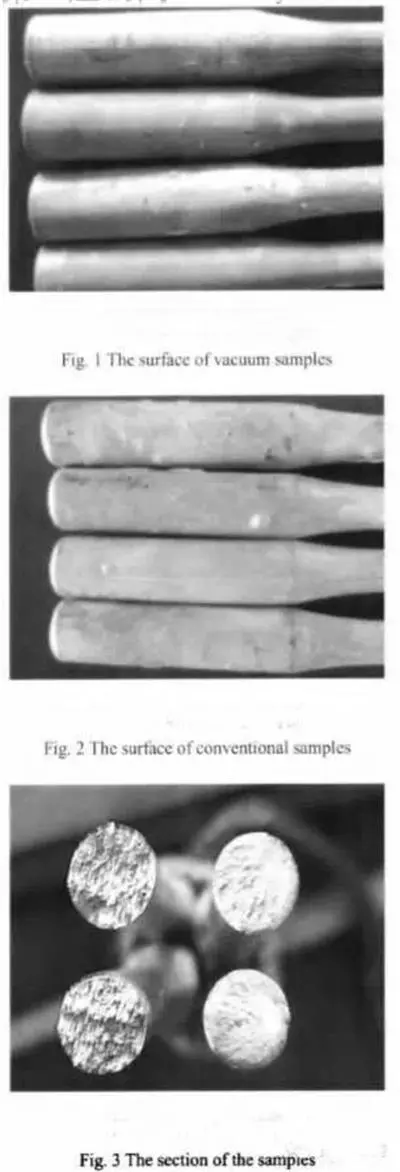
2.2. Mechanical properties
Using T6 heat treatment, namely using solid solution and artificial aging method to understand the difference between the common die casting process and the gas content of die casting process of vacuum die casting process.
Two kinds of samples were randomly selected to do mechanical performance test.
The test results before heat treatment are shown by table 2:
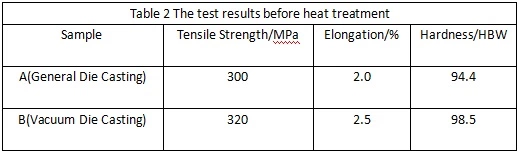
From the test results of Table2, the mechanical properties of the two samples were not quite different before the heat treatment, and the mechanical properties of the vacuum die casting samples were slightly better. The tensile strength increased by 6.67%, the elongation increased by 25% and the hardness increased by about 4.34%. This is because there are more pores in samples of conventional die casting, coarse grains in the organization, the organization is relatively loose; and vacuum die casting in the sample porosity less grain structure in small tissue is relatively dense.
Solid solution and artificial aging treatment were carried out for two samples at the same time. The solid solution conditions: the temperature is 515 degrees Celsius, the time is 6 h, the cooling way is 90 degrees Celsius, the artificial aging condition: the temperature 175 degrees Celsius, the time 6 h, the cooling way is the air cooling. The interval time between solid solution treatment and artificial aging treatment was 1h.
According to the above conditions, after the solid solution and artificial aging treatment, the mechanical properties of the samples were detected, and the results are shown in table 3.
Data from table 3 shows, after T6 heat treatment, the mechanical properties of vacuum die casting sample is still in good condition, but the elongation is 180% higher than the cast; and the mechanical properties of conventional die casting samples decreased greatly. After T6 heat treatment, while two kinds of eutectic silicon die casting in the organization is refined, but pore size and vacuum die casting in the sample has not changed significantly; while conventional die casting in the sample due to pore volume expansion increased significantly, resulting in the mechanical properties decreased greatly.
Table 4 shows the two test results of die casting process of die casting gas content It can be seen from table 4 that the gas content of the vacuum pressure casting is really less than that of the ordinary pressure casting.
Due to the air in the mould is drown out when vacuum die casting, the probability of air hole defects is reduced greatly, and the micro-structure of the casting is improved, as well as the mechanical properties of the castings are improved.
3. Average passing rate comparison
According to statistics, in 2007 OPW series of products, the average pass rate is just over 60% a little, disqualification mainly caused by air hole defects. In 2008, the vacuum die casing was made by selecting the 633F-2 type rapid joint, and the qualified rate of the first batch of die casting was obviously improved, reaching up to 84%, single batch of die casting reach up to 97.36%. In 2007 the average passing rate only reach69.79%, in 2008 the average passing rate reached 89%, the product passing rate increased by about 28%.
By the end of 2009, OPW series quick connector has 9 types of products made of vacuum die casting mould. The 9 models have large dosage. The passing rate of ordinary mould casting is low.
After changing into a vacuum mold, the passing rate increases a lot.Figure 4 shows the monthly qualified rate of the 2008 and 2009 OPW series of products. It is seen from the figure, the application of vacuum die casting technology, product qualification rate is stable at more than 80%. Due to the substantial increase in product qualification rate, the production efficiency is improved, the production costs are reduced, thereby enhancing the competitiveness of the market.
4. Conclusion
1). Tensile strength test, compared with conventional die casting samples, sample grain section of vacuum die casting is more fine, its color is closer to Aluminum Alloy color; after T6 heat treatment, the surface of the drum vacuum die casting specimen bubble less, measuring samples at the same diameter of the specimen the increase of more than 0.1mm, and the vacuum die casting samples almost has no change.
2). Mechanical properties of the vacuum die casting specimens are slightly better than those of the ordinary die cast specimens. The tensile strength increased by about 6.67%, the elongation increased by 25%, the hardness increased by about 4.34%. After T6 heat treatment, the mechanical properties of vacuum die casting samples remain in good condition, and the elongation is 180% higher than the cast, while the mechanical properties of conventional die casting samples decreased greatly.
3). Vacuum die casting technology not only can improve the surface finish, reduce the porosity defects, but also improve the average qualified rate of castings. Among them, the average pass rate of 633F-2 type rapid joint can reach 89%, compared with the normal die casting process, the product pass rate increased by about 28%.