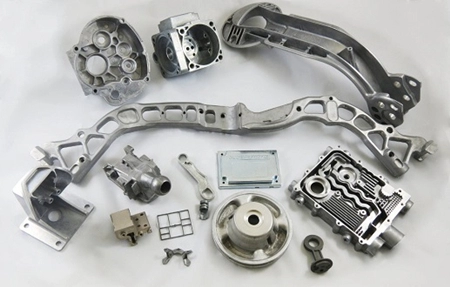
The die-cast in aluminum alloy ADC12 has light weights, good thermal conductivity and corrosion resistance, which meets the requirements for lightweight, energy saving and emission reduction of automobiles. Therefore, automobile transmission's cover parts made from aluminum alloy by die casting process is a development trend. However, various surface defects easily occur on workpieces made from aluminum alloy, which are mainly black spots. There was literature on black spots on the surface of aluminum alloy flange forgings, determining that they were caused by organic medium pollution.
A gearbox manufacturer has a die-cast and machining production line for cover parts of automobile transmission. The materials used for transmission and clutch's cover parts are aluminum alloy ADC12. However, black spots are prone to appear on surfaces of die-cast aluminum alloy cover parts during the manufacturing and storage process.
According to the actual production situation and storage conditions of the aluminum alloy workpiece on site, combined with analysis methods such as scanning electron microscopy, surface morphology and composition of different types of black spots are analyzed and influence mechanisms of each link of the production process on black spots are discussed in this article. Specific process optimization measures are proposed to achieve the purpose of reducing black spots and improving product quality based on the influence mechanism of defects.
1.
Preliminary analyses
The morphology of black spots of
die-cast aluminum alloy ADC12 cover parts during processing and storage is mainly divided into two categories, and the macroscopic morphology of the two is shown in the Figure 1. It can be seen from the Figure 1 that the first defect is a continuous flake black spot, and its color is significantly darker than the normal area; the second defect has a macroscopic appearance of white or gray powder, and dot-like black spots appear after removing the powder. The main production processes of the aluminum alloy cover part are: die casting→shot blasting→machining→cleaning→drying→storage. The main production processes and other conditions of the two types of black spots are compared in the Table 1.
Figure 1 Macroscopic morphology of black spots
Table 1 A comparison of the two types of black spots
2.
Microstructure observation and energy spectrum analyses
Both types of black spots occur on the non-machined surface of aluminum alloy parts. Take one sample of normal non-defective non-machined surfaces and two samples for the two different defects. Clean the three samples in petroleum ether, and then observe the morphology of black spots by field emission scanning electron microscope. The three microstructures are shown in the Figure 2.
Figure 2 Morphology of SEM microstructures
According to the Figure 2, it can be seen that the normal non-machined surface of the aluminum alloy workpiece is shot blasted, and the surface is relatively dense under the action of steel shot blasting. However, there are many pits caused by steel shot blasting, and the overall appearance is not smooth. Flake or granular debris was distributed on the normal surface at high magnifications. There is no obvious difference between the microscopic structure morphology of the first defect and the normal surface, and the pits and debris caused by the shot blasting process are retained. The white adhered micro-morphology of the second defect shows granular debris. After the white adhesive substance is removed and ultrasonically cleaned, the micro-morphology of the substrate is significantly different from the normal surface, showing a small-sized porous net structure. EDS energy spectrum analysis was performed on each characteristic area of the normal and defect surfaces respectively, and the analysis results are shown in the Figure 3.
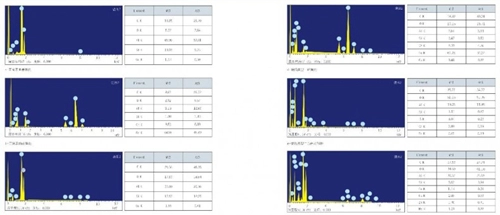
Figure 3 results of EDS energy spectrum analysis
It can be seen from the EDS testing results that the main component of the normal surface matrix is the original composition of aluminum alloy ADC12. In addition, it also contains a certain amount of C and O elements, which may come from the organic industrial media that the workpiece is in contact with in the processing process. The media pollute and slightly oxidize the workpiece. The composition of debris on normal surfaces is completely different from that of the matrix. The main element is Fe, and there is a high content of Cr. It can be inferred that the steel shot's debris which is difficult to remove is generated in the shot blasting process.
Compared with the normal surface, the matrix and debris of the first defect contain more C and O elements, which are contaminated by organic industrial media more serious. In addition, the content of Si in the matrix of the first defect is significantly increased.
Because the first defect mainly occurs after the die casting process, it can be inferred that it is caused by the adhesion of organic matter generated in the die casting process by synthesizing its microscopic surface morphology. The industrial medium that the workpiece is in contact with in the die casting process is a mold release agent. The main component of mold release agents used for the aluminum die-cast is silicone oil. Combined with high silicon content at the surface matrix of the first defect, it can be further concluded that the first defect is caused by the accumulation adhesion, oxidation and discoloration of the mold release agent containing silicon in the die casting process.