Abstract: By using simple round tensile specimen, we studied the effects of pouring temperature on properties of ADC12 alloy super slow speed die castings to optimize the super slow speed die casting technology and its parameters. The results showed that the density of castings was higher than that of ordinary die castings under the super slow speed test condition. The pouring temperature had the optimum value, which was related to mold temperature and mold release agent. Under the super slow speed standard test condition, the optimum pouring temperature was 700 ℃. At this time, the primary α-Al in the alloy was dendritic, and the primary and secondary dendritic arms were obviously smaller or shorter with better casting properties compared with those under the higher pouring temperature condition.
The hole defects are one of the most important defects in the die castings. The gas produced in the flow and the shrinkage happened in the solidification process of molten metal in the aluminum alloy are the main reasons for the defects of the hole type. Super slow speed (SSS) die casting is the method which fills the die casting mold cavity with liquid metal under the laminar flow on the high pressure condition(50~120 MPa), and the liquid metal quickly solidifies under pressure so as to get die castings with low gas content. (The gas content is controlled between 0. 6 and 0. 8 ml per 100 gram of die castings while the gas content in the ordinary die castings is 25 ml per 100 gram).
In the process of die casting, temperature, as a technological parameter of thermal specification, plays an important role in the process of mold filling, the thermal condition of mold and the efficiency of operation. The temperature mentioned in thermal specification in the process of die casting refers to the alloy pouring temperature and mold temperature. Domestic and foreign scholars have conducted lots of researches on the technological conditions' influences on the properties of die castings under common technological conditions. However, we have never read any reports about studies of SSS die casting technology. Putting ADC12 as the object, we designed the standard tensile test rod metal mold and carried out the SSS die casting test in this study. This research studied the effects of different mold temperatures and alloy pouring temperatures on the properties of super slow die castings from the perspectives of density, mechanical properties and microstructures of die castings.
1
Test Method
1.1 Test Materials
Selecting commercial
die casting aluminum alloy JIS (Japanese Industrial Standard) ADC12 as test materials, the chemical composition was determined by ICP as follows: 11.25% Si, 3.09% Fe, 2. 51% Cu, 0.21% Mn, 0.096% Mg, 1.74% Zn, and the remaining Al. ADC12 belongs to the eutectic alloy with the eutectic temperature about 577 ℃, liquidus temperature 580 ℃ and solidus temperature 515 ℃.
1.2
SSS Die Casting Technology
According to the specifications of GB/T6397, in this project, we designed and made the mold for SSS test and studied the effects of pouring temperature on microstructure and properties of die castings through this mold. The samples were put in a 6500 KN cold chamber die casting machine (TOYO BD-650-V4-N) with a pouring gate size of 24 mm x 2 mm and an overflow slot size of 20 mm x 3.0 mm, casting speed of 0.09 m/s(039 m/s of gate), much faster than the ordinary die casting, the pressure of 100 MPA, the mold temperature of 150 ℃, the holding time of 10s, the degassing time of 20 minutes, the handle thickness of 40 mm, the special SSS release agent (with the water ratio of 1: 30) and the punch lubricated by slow speed lubrication. Set the pouring temperature as 675℃, 690℃, 700℃, 720 ℃. Change the mold temperature or release agent. Adjust the experimental values of pouring temperatures accordingly (see Table 1).
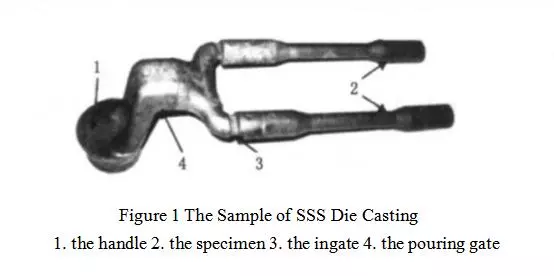
Table 1 Effect of Pouring Temperature on Micromicrostructure and Properties of Die Castings
1.3 Test & Detection
Removing the specimen from the runner , then tested the density of the specimen under different test conditions (JT5003 type electronic balance, accuracy ± 0.001 g) and its mechanical properties (CSS-2220B electronic universal testing machine). The matallographic specimen was cut and then made from the die casting, and its microstructure was observed on a DMM-400C metallographic microscope. The strain rate was controlled at about 1 mm / min in the tensile test on a universal testing machine. We tested 3 to 5 samples under the same technological conditions and took the average value as the final measurement result.
2.
The Test Result and Discussion
2. 1 Microstructures of ADC12 Alloy SSS Die Castings at Different Pouring Temperatures
If ADC12 alloy was casted under the normal temperature (660 ~720 ℃), the primary α-Al were usually dendrites. As the casting temperature changes, the solidification morphology of primary α-Al also gradually changes. Figure 2 is the microstructure of the core of ADC12 alloy under different pouring temperatures. When the pouring temperature was 720 ℃, the primary α-Al in the ADC12 alloy presented a developed dendritic morphology, with very coarse dendritic arms and a few spherical or granular primary α-Al in the tissue.(See Figure 2d) The white region was primary α-Al, the dark α-Al + Si eutectic microstructure and a small amount of polygonal block AlSiFeMn quaternary phase. When the pouring temperature was 700 ℃, the primary α-Al in the ADC12 alloy developed from the dendritic like form into a rose like form and more spherical or granular primary α-Al appeared in the organization with a very uniform distribution. (See Figure 2c) When the pouring temperature was 690 °C, the primary α-Al in the ADC 12 alloy remained dendritic, and the primary and secondary dendritic arms were significantly smaller or shorter than those under the higher pouring temperature.( See Figure 2b) When the pouring temperature was further reduced to 675 ℃, the primary α-Al morphology in the ADC12 alloy had not been further improved, but the larger dendritic α-Al grains appeared in the microstructure and even were coarser than the microstructure of specimen under higher pouring temperature.(See Figure 2a)
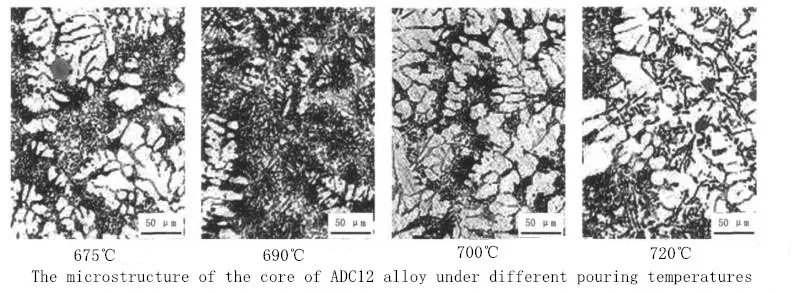
It can be seen from Figure 2 that the primary α-Al in the ADC 12 alloy tended to appear in the dendritic form, and the eutectic Si presented in the form of needle or sheet.
As the ADC12 alloy was of high content of Si and high solidification latent heat, the alloy melt can transfer more physical heat to the mold under the higher temperature condition. The mold being heated to a higher temperature reduced the average cooling speed in the alloy solidification process and lengthened the solidification time of the blank. Since the growth time of the primary α-Al and the eutectic Si was lengthened, the primary α-Al in the die castings appeared in coarse dendrites and eutectic Si was in a large needle-like presence at the higher pouring temperature.
As the pouring temperature decreases, the physical heat of the alloy melt transferred to the mold decreases at the time. Before the solidification of the alloy, the mold was only heated to a low temperature, which leaded to the faster cooling speed of the alloy solidification and shorter growing time of the primary α-Al. The primary α-Al could not appeared in the developed dendritic form and finally formed in rose-like dendtries. As the ADC12 alloy quickly solidified on the high pressure, the pressure just acted on the die casting and caused a large-scope solidification. If the pouring temperature is low, the condensate latent heat release will certainly produce a more uniform temperature field, which will help the fusing of secondary arm root of rose-like primary α-Al and accelerate the formation of spherical or granular primary α-Al. If the pouring temperature is too low, the alloy in the pressure chamber and the runner can be precipitated a small amount of primary α-Al. The primary α-Al precipitated before solidification will further grow in the solidification process under pressure, which will bring some coarse primary α-Al dendrites in the microstructure.
2.2 The Properties of ADC12 Alloy SSS Die Castings under Different Temperatures
As the selection of pouring temperature is related to many factors, in this project, we not only studied the pouring temperatures' effects on the properties of die castings on the SSS standard test condition, but also studied the effects of factors like mold temperature, the mold release agent and pouring temperature on the properties of die castings. The results of the test are shown in Table 1.
As SSS die castings have poor filling properties, properly increasing the pouring temperature can improve the casting properties when voltage-withstand die castings with thick wall were made, but the pouring temperature can not be too high. It can be seen from Table 1 that as the pouring temperature increases, the density and mechanical properties of castings were increased and improved first, then reduced and dropped, finally reaching its maximum when the temperature was 700 ℃. On the one hand, hydrogen can be easily absorbed into the aluminum alloy when it is melting and the solubility of hydrogen will be increased exponentially with the increasing of temperature. Thus, the higher the pouring temperature is, the more hydrogen in the alloy is dissolved and the more the stomata and oxide the die castings contain. On the other hand, the coarse dendrites of primary α-Al will also reduce the properties of die casting, which means the high pouring temperature will also reduce the properties of die castings. But if the pouring temperature is too low, not only a small amount of silicon will be precipitated as the free existence in the die casting and deteriorate the properties, but also the primary α-Al dendrities will be very thick, which means too low pouring temperature will reduce die castings properties.
The temperature of the die casting mold directly affects the qualities and productivity of die castings. In each production cycle, the heat transferred from the molten metal to the mold should be balanced with the heat dissipated of the mold and transferred through the cooling system. When the mold temperature is high, the lower pouring temperature can be selected, which helps to quickly solidify the castings and obtain fine solidified microstructure so as to gain better mechanical properties. In the die casting process, the mold is constantly heated by high-temperature liquid metal, making the temperature of mold continue to rise. Too high mold temperature will cause some defects of die castings, such as sticky mold, bubble, crack and hot crack, etc. Except this, the material strength of molds working for a long time in the high temperature environment will decrease, resulting in appearance of mold surface cracks and shortening service life of mold. In order to alleviate and solve the above problems, in the die casting process, except selecting the correct casting temperature and adjusting the mold temperature with the help of mold temperature adjustment machine, we often use spraying or coating release agent and anti-sticking measures to relieve the mechanical impacts and frictions between the die castings ( die casting alloy) and mold cavity surfaces. It can be seen from Table 1 that it is appropriate to use release agent of low concentration under the high pouring temperature condition.
3.
Conclusion
(1)SSS die castings are of less gas content and high casting density.
(2) The properties of castings are greatly affected by the pouring temperature, first improving and then degrading with the increase of pouring temperature.
(3) The optimum pouring temperature is related to the mold temperature as well as the release agent. Under the SSS standard test condition, the optimum pouring temperature was 700 ℃. The primary α-Al in the alloy were dendrites and the primary and secondary dendritic arms were significantly smaller or shorter with better die casting properties compared with those under the higher pouring temperature condition.