In recent years, the demand for large-scale die-cast molds is increasing due to the continuous development of the domestic automobile industry, and the requirements for the yield, production efficiency, manufacturing cost and reliability of such molds get higher. The multi-slide nested core-pulling mechanism and cooling system of the mold are introduced in this subject based on the structural characteristics of the shape and hole position of a certain automobile transmission housing, starting from the design of the gating system of the die casting part. Finally, a qualified product is obtained.
1.
The product structure analysis of gearbox housings
Figure 1 is the die casting part of a certain type of automobile gearboxes. The material is ADC12 aluminum alloy. The outline size is 550 × 444 × 301 mm, and the total mass is about 27.3 kg. It is a large-scale die casting part. This product has a complex structure, with many ribs and holes. The main wall thickness is 7 mm and the wall thickness is uneven. It can be seen from Figure 1 that the outer side of the product has holes, and the slide block structure needs to be designed in the 4 directions of the mold. It can be seen from Figure 1a that the product has a large number of holes, with thicker walls in partial areas, and high air tightness requirements for the bearing holes and cylinder holes are put forward. It can be seen from Figure 1b that there is a deep cavity structure inside the product, and the center part of the large bearing hole at two sides cannot be manufactured by the die casting process, which requires complete filling and needs to be connected to the bottom. Later, it needs to be processed by machining. After this part is connected, there is a greater risk of internal defects due to the deep cavity and wall thickness problems. This is difficulty 1. In addition, there are many dense side holes. When the cooling system of the mold is arranged, it is difficult and complicated. At the same time, there are 8 threaded holes that are different from the direction. There is an included angle between the two and it is impossible to loose core in the same direction. It is necessary to design the core-pulling mechanism separately to ensure the internal quality. This is difficulty 2. See Figure 1b and Figure 1c.
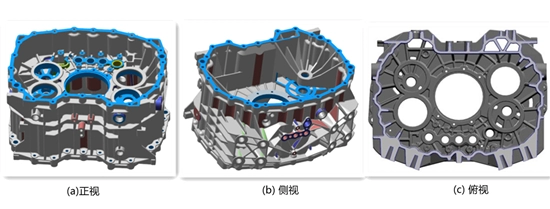
Figure 1: The three-dimensional model of the gearbox housing
2.
The design of the gating system
The product's structure and gating system play a decisive role in the mold's structure. A reasonable gating system can not only ensure the quality of the
die casting part, but also simplify the mold. In order to solve the difficulty 1 and ensure the internal quality of the large bearing holes on both sides, small improvements were made to the product (Figure 2); a small dense grid was added on the surface of the bearing hole to alleviate the surface defects of the die casting, especially the gas hole and increased surface area, thereby increasing the heat dissipation surface and improving the efficiency of the heat dissipation.
The gating system is designed on the end faces (machined surfaces) of the large bearing holes on both sides (see Figure 2), and a branch is specially designed to fill the large bearing holes at a distance to ensure the internal quality of the bearing holes; set a slag collector at the distant or gathering part of the die casting part, ensuring that the remote cold material, gas, and slag inclusion can flow as much as possible to eliminate defects of die castings. In addition, this gating system can be removed by using a mechanical electric saw or subsequent trimming die, and the remaining pouring riser can be removed by machining; the appearance of the die casting is good.
After adopting this kind of gating system, the mold's parting surface can only be selected close to the end faces of the large bearing holes on both sides. The shallow cavity on the front is designed on the fixed mold, while the deep cavity on the back is designed on the movable mold. Four sliding blocks at the up, down, left, and right of the four sides. The complex side shown in Figure 1b is located at the bottom of the mold.
3.
The design of the mold
3.1
The structure design of the sliding block
According to the structural characteristics of the die casting, in addition to the movable and fixed molds, the mold is divided at the ribs around the die casting part (Figure 3). The ejection direction angle of 8 threaded holes and the bottom are inconsistent. The mold is designed as a pin. The sliding blocks 5 and 6 are designed, using a nested core pulling mechanism with multiple sliders, which is also called a two-stage linkage core pulling mechanism. Using their respective driving elements, when the mold is opened, the side sliders 5 and 6 are first drawn, and then the slide block 1 is drawn to complete the opening of the mold. When the mold is closed, the large sliding block 1 is reset, and then the small slide block is reset.
3.2
The structure design of the secondary core pulling
Figure 4 shows the structure of the lower sliding block of the housing, and Figure 5 shows the action process of the secondary core pulling. After the die casting part is formed, the mold is opened, and the mold opening force makes the inclined pin and the inclined hole of the side sliders 5 and 6 move relatively. Since the side slider is installed in the bead groove of the movable template in the form of clearance fit, the side slider is driven to move outward. After moving to the core-pulling, the side core-pulling and mold's opening are completed. At this time, under the action of the limit block, the side slider accurately stays at the end position when the slider is puled by the oblique pin so as to prevent the oblique pin and oblique hole from being misaligned for closing the mold next time as well as the occurrence of a collision.
When the mold is closed, the inclined pin accurately enters the inclined hole of the side slider and makes the reset action happen. However, positioning by the inclined pin only is very difficult, and the locking action of the inclined pin will cause the side slider to retreat when it is impacted by the high pressure of the injection pressure. Therefore, the locking device of the side slide block should be designed, namely the wedge block, and its inner side is in contact with the tail of the small slide block with an inclined surface to ensure the precise positioning of the side core and lock the side slide block to prevent displacement or retreat caused by side injection pressure.
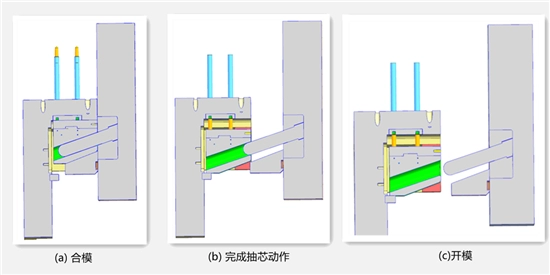
Figure 5 The process of the secondary core pulling
3.3
The design of the mold's cooling system
The mold's cooling system plays a key factor in quality of the die casting part, the mold's service life and production stability. In order to ensure the internal quality of this die casting part, various types of waterways are designed around the mold and its upper and lower positions, as shown in Figure 6. It can be seen from Figure 6a that large circulating cooling is designed on the movable and fixed molds, and point cooling or high pressure cooling is designed for the deep cavity parts to eliminate the problems of shrinkage, cracks and mold sticking caused by partial overheating as much as possible. The sleeve-type core-pulling mechanism results in a small space when the large circulating cooling water is arranged. Only one set of circulating cooling is designed on the periphery, and multiple point cooling is designed at the overheating position. Because the deep cavity has few positions and holes as well as simple structure, multi-layer circulating cooling is mainly selected to ensure the stability and balance of the mold temperature. It can be seen from Figure 6b that a complex set of cyclic cooling is designed on the two secondary core-pulling mechanism, which can not only cool each pin, but also cool the inclined core pulling mechanism, so that the core pulling mechanism works smoothly and has low malfunction rates and high production efficiency.
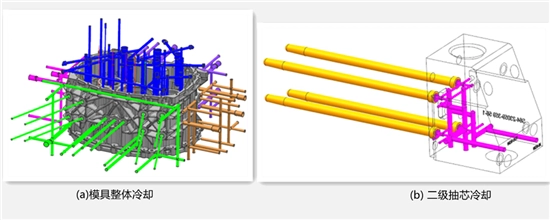
Figure 6 The design of the cooling system
4.
Production verification
The mold was made by using the above-mentioned design scheme, and production was carried out. Figure 7 is a photo of qualified products of die casting parts. After machining the bearing holes on both sides and the 8 threaded holes at the bottom of the product, there are no obvious defects. Through actual production verification, this structural mold can solve the problem of different core-pulling directions on the same side. The core-pulling is stable and the ejection is safe. The quality and size of the die casting part can meet the requirements for the product, and mass production has been performed.
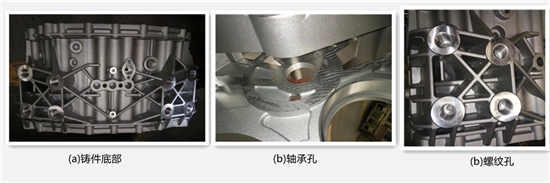
Figure 7 Qualified products