Dedicated Die-cast Aluminum Alloys for Super-large Thin-walled Body Structural Parts
The body structural parts such as shock absorption towers, A or B columns, cross beams and door inner panels are frames of car bodies, and as skeletons that support car bodies, they are the first guarantee for the safety of cars. Such parts usually have large sizes and complex structure. Therefore, traditionally designed structural parts are mostly made by stamping and welding the steel plate, and then several parts are assembled.
With the continuous advancement of automobile lightweight technology, especially the continuous improvement of ultra-high vacuum high-pressure casting technology and the emergence of ultra-high tonnage giant die-casting machines, high-pressure die casting aluminum alloy body structure is increasingly used to replace the structural part by stamping and welding the steel plate. The typical high-pressure casting
aluminum alloy parts are shown in the following pictures.
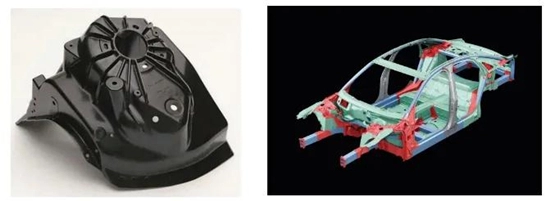
The shock absorption tower The typical aluminum alloy car body structural part
Adopting ultra-high vacuum high-pressure casting aluminum alloy structural parts must first solve the following two problems:
- Usually, the body structure parts have large sizes and complex structure; the wall thickness is usually only 2 to 3 mm, so aluminum alloys need to have excellent casting performance.
- Aluminum alloy body structural parts require aluminum alloys to have good elongation and high strength to meet requirements of safety performance (the crash test) and connections of parts.
Conventional parts produced by ultra-high vacuum die-cast technology usually adopt AlSi10MnMg aluminum alloys and require T7 heat treatment to obtain the required performance; heat treatment will cause deformation of the part, and the part needs to be adjusted. Complicated heat treatment and adjustment processes lead to high costs of such high-pressure die-cast aluminum alloy parts. Therefore, they are currently only used in mid and high-end models, such as NextEV ES8, Cadillac CT6, BMW's 5 and 7 Series, and Benz's class C.
The rapid development of electric vehicles is rapidly driving the large-scale application of high-pressure casting aluminum alloy body structural parts, making ultra-high vacuum high-pressure casting production technology more used in China. When Tesla made the giant ultra-high vacuum high-pressure casting aluminum alloy parts of one-piece rear floors public, people in the industry were shocked. To obtain the casting of such large-size parts, only aluminum alloy casting materials without heat treatment can be used to avoid the problems of the part's deformation and bubbles caused by heat treatment. Although many domestic die-cast plants have fully mastered the ultra-high vacuum high-pressure casting production process, they do not have the technology and experience of alloys without heat treatment; they cannot produce integrated large-scale body structure parts.
The EZCAST™ series alloy was successfully developed in the 1990s and successfully applied to the structural parts of the Audi A8's all-aluminum body. After market applications, continuous optimization and improvement for more than 10 years, the series of alloys which can be customized, manufactured and meet the customer's mechanical performance requirements are gradually formed. The properties of the typical alloy C611 of the EZCAST™ series are as follows:
Casting performance
C611 is a high-performance Al-Si die-cast aluminum alloy dedicated for lightweight and thin-walled structural parts of automobiles. The silicon content of C611 alloy is equivalent to that of the most widely used cast aluminum alloy A356, and it has very good fluidity. It has been widely used in the production of thin-walled structural parts such as shock-absorbing towers by many die-cast manufacturers in Europe and the United States for many years. It is generally believed that the wider the solidification temperature range of the alloy is, the greater the tendency of heat rates and solidification shrinkage becomes. Compared with traditional die-cast aluminum alloys, C611 alloy does not contain copper and zinc alloy elements that are easy to form low melting point eutectic, so the solidification temperature range is only about 60℃. For comparison, the solidification temperature range of conventional untreated alloys is greater than 100°C, while that of A380 alloy is as high as over 150°C. Therefore, C611 alloy has a very small tendency to heat rates and solidification shrinkage. The sticking tendency of die-cast alloy depends on the tendency of the aluminum alloy having a chemical reaction with the die-cast mold's material in the liquid and solid-liquid two-phase region, usually H13 die steel. The content of iron and manganese has a great influence on this tendency. Advanced material design methods are used to optimize the composition of C611 alloy, so that it has excellent anti stick ability while obtaining the best mechanical properties.
Mechanical performance
C611 alloy can obtain very good elongation in the as-cast state, and meets some special performance requirements that can be achieved by heat treatment of automotive structural parts in the current domestic and foreign markets, such as good bending performance and automatic riveting performance. The following table shows the mechanical properties that C611 and C611M can achieve in the as-cast state and after baking finish treatment.
Table 1 Mechanical properties of C611 and C611M alloys
Alloys |
Sources of samples |
Yield
Strength
(MPa) |
Ultimate
Strength
(MPa) |
Elongation
(%) |
C611 |
A die-cast sample of 3 mm, as-cast |
123 |
268 |
16.2 |
C611 |
A sample of a C611 shock absorption tower casting body, as-cast |
117 |
268 |
14.1 |
C611 |
A die-cast sample of 3 mm |
159 |
275 |
12.4 |
C611M |
A die-casting sample of 3 mm, as-cast |
128 |
275 |
14.0 |
C611M |
A die-cast sample of 3 mm |
175 |
288 |
10.9 |
C611 alloy has been applied in major domestic aluminum alloy body structure die-cast plants with good results. As major main engine plants increasingly put forward requirements for the cost reduction of body structural parts, it is an inevitable trend to use cast aluminum alloys without heat treatment to produce body structural parts; and as the application of giant integrated body structural parts matures, adopting cast aluminum alloy without heat treatment is an inevitable trend.