First, when the
scaling defect occurs, check the changes in the workshop such as aluminum water temperatures, mold release agents, cooling water temperatures, etc. to see if there are variables that affect scaling of the die casting. Second, check and analyze locations, shapes, areas, proportions and color changes of scaling so as to determine the specific cause of the scaling and specific solution. The solutions to scaling of
die castings are as follows:
(1) The gating system of the mold should be optimized to make the molten metal flow suitable, without long-distance flow, and not converge at locations where they are far away from the inner gate.
(2) The size and proportion of the gating system of the mold should be appropriate; the thickness, cross-sectional shape and size of the runner should be slow and uniform, and change the corner. There should not be sharp and dead corners, so that the molten metal flows smoothly and continuously. Eliminate the surface crust formed by too fast surging molten metal, splashing premature punching or turbulent flow.
(3) The mold design should meet the model requirements. Each die casting machine has its own requirements. Deformation should not occur. Deflection may occur during pressurization.
(4) Check the overall size and rigidity of the mold; check whether the mold has sufficient support; whether it is necessary to strengthen the mold strength and tighten the mold components; the movable mold side must have a large column with enough support, and at the same time, reduce the injection force, high speeds and instant impact force.
(5) Check whether the cooling water path of the mold is too close to the scaling part to prevent excessive cooling. If the mold structure allows, properly improve capacity for slag discharge and exhaust, and try to arrange the slag bag near the scaling area. If there is a slag bag, increase the width and thickness of its overflow. In this way, not only can the chilled aluminum water in the cavity be discharged into the slag bag, but also the back pressure in the cavity can be reduced, thereby improving the filling performance of the aluminum water.
(6) Regularly clean the mold cavity and trimming in the pressure chamber in the production process. The position, method, standard and frequency of mold cleaning must be clearly defined in the work instruction, and relevant training should be done by preferably someone responsible.
(7) Check whether the clamping force adjustment of the die casting machine is appropriate. If the setting is too great, it will seriously affect the service life of the mold; if the clamping force is insufficient, the flying material will be serious, which will have a great impact on product quality and personal safety.
(8) Due to the structural limitations of the product itself, the castings have thick and hot spot parts. First, when developing new projects, you need to communicate with customers to optimize the wall thickness of die castings and change the structure of hot spots to eliminate the hot spots. If the casting structure cannot be modified, you need to minimize the pouring temperature and mold temperature.
(9) Scaling caused by the molten metal sticking to the mold or shrinkage will occur at the direct punching part or near it. Therefore, the following points need to be carried out: a. Check the iron content of the raw material and try to control it between 0.6% and 0.9%; reduce the sticking performance of aluminum water; b. Polish the surface of the mold to temporarily eliminate the sticking; c. Increase the partial demolding angle to facilitate demolding; d. Choose the appropriate release agent for different types of products, and increase the concentration of demolding and the amount of spraying to prevent sticking; e. Increase hardness of the surface of the mold, and it can be treated with nitriding or surface coatings to prevent sticking; f. The parts that are easy to stick to the mold can pass cooling water or design high pressure point cooling.
Shrinkage cavities are prone to appear at the final solidified part due to improper product structure design, uneven wall thickness and large partial hot spots, as shown in the Figure 1.
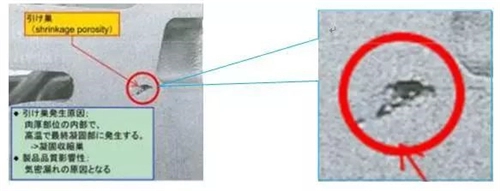
Figure 1
The X-ray inspection, polishing and corrosion state of the shrinkage part of the product is shown in the Figure 2.
Figure 2
Observe the microstructure of shrinkage cavity with a microscope as shown in the Figure 3. This internal defect can easily lead to leakages of products that require airtightness, such as air-conditioning compressor products.
Figure 3
In order to effectively solve the above problems, the extrusion pin is designed to prevent shrinkage. If the partial extrusion design and use are improper, it is likely to cause the product to peel after shot blasting. At this time, we need to optimize the extrusion pin structure.