Compared with other manufacturing processes, the die casting process has high production efficiency, high dimensional accuracy, excellent mechanical properties, good material utilization, and better economic benefits for mass production. Among aluminum alloys for automobiles,
die-cast aluminum alloys and other cast aluminum alloys account for about 80%, and processed aluminum products such as plates, strips, foil, tubes, rods, wires, forgings, powders, pastes, etc. account for only about 20% . The consumption of die castings accounts for about 70% of the total consumption of casting products, so die-cast aluminum alloy products account for about 54% to 70% of aluminum in automotive .
Since 2009, China's automobile sales have occupied the world's first place for eight consecutive years, from 13 million in 2009 to over 27 million in 2019. With the increasingly fierce competition in the automobile market, various manufacturers are moving towards directions such as good quality, good reliability, light weight, energy&conservation, environment protection and low costs. Moreover, as automobile emission standards and international environmental protection policies become stricter year by year, new energy vehicles have become the key development direction of the future automotive field. New energy automotive structural components with good strength and quality, such as the automobile body, chassis, shock absorber, etc. are increasingly required to be manufactured by die casting. All these show that the aluminum alloy die casting has an important position in the die-casting industry and is the mainstream of the die casting industry.
Process characteristics of die-cast aluminum alloys
In addition to better die casting process performance and better mechanical properties, die-cast aluminum alloys also need to have the following process properties:
①
Aluminum alloy die castings should have good thermoplastic rheological properties. They should have good thermoplastic rheological properties when the superheat is not high and near the liquid and solidus temperature to achieve the filling of complex cavities, form a good casting surface, and avoid shrinkage cavity defects.
②
Aluminum alloy die castings ought to have small linear shrinkage rates, avoiding cracks and deformation during die casting and improving the dimensional accuracy of products.
③
Aluminum alloy die castings are supposed to have the small solidification temperature range so as to obtain rapid simultaneous solidification and reduce the amount of defects like internal shrinkage holes.
④
Aluminum alloy die castings need to have good high-temperature thermal strength to avoid heat cracks or serious deformation when the mold is opened.
⑤
Aluminum alloy die castings require to have good casting performance, no chemical reaction with die casting molds, and the feature of not being sticky to prevent the aluminum alloy sticking to the mold.
⑥
Aluminum alloy die castings should have good physical and chemical properties, and they should not easy to take in gas and oxidize in the high-temperature molten state. They can meet the heat preservation needs of the die casting process for a long time.
Die-cast aluminum alloy classification
According to alloy composition,
die-cast aluminum alloys can be divided into four series, including Al-Si (Al-Si-Cu, Al-Si-Mg), Al-Cu, Al-Mg and Al-Zn. Al-Si die casting alloys are most widely used due to their small crystallization temperature interval, great silicon phase solidification crystallization latent heat and specific heat capacity, small linear shrinkage, good flow properties, good filling properties, small heat crack and shrinkage cavity tendency. Although the Al-Cu die casting alloy has high mechanical properties, the addition of Cu element reduces the corrosion resistance of the material, and the service life of die casting products is greatly reduced. Moreover, the die casting process is prone to segregation and cracking, so the application range is small. Compared with Al-Si series die casting alloys, Al-Mg series die casting alloys have poor casting performance, great fluctuations in mechanical properties and great wall thickness effects, a greater tendency to stress corrosion and easily crack during die casting. Although Al-Zn series die casting alloys can obtain better mechanical properties after natural aging, their corrosion resistance is poor; they are prone to heat cracks and stress corrosion, so they are less used. Table 1 shows the grades, chemical composition and mechanical properties of commonly used die-cast aluminum alloys. Among them, Al-Si-Cu alloys such as AlSi9Cu3 (A380) and AlSi11Cu3 (ADC12) are the most widely used. As shown in the table below, Si, Cu, Mg, Mn, Fe, Ni and rare earth elements are generally added to die-cast aluminum alloys.
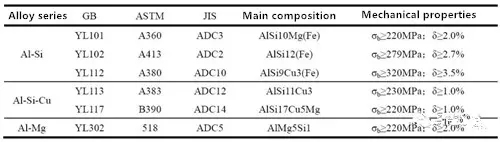
Table 1 Grades, chemical composition and mechanical properties of Al-Si, Al-Si-Cu, Al-Mg
Typical applications of die-cast aluminum alloys
At present, the scope of application of aluminum alloy die castings in the automotive industry at home and abroad is classified according to their use functions. They have been used in structural parts, stressed parts, safety parts and decorative parts, mainly including the following aspects:
①Power systems: cylinder blocks, cylinder covers, cylinder head covers, crankcases, oil pans, pistons, pump bodies, pump covers, inlet pipes, generator housings, engine gear rooms, six seat rocker-arm supports, various supports of engines, etc.
②Transmission systems: gearbox housings, gearbox oil circuit boards, clutch housings, shift forks, gearbox brackets, etc.
③Steering systems: rack covers, rack housings and turbine housings
④Chassis assembly: suspension brackets and beams
⑤Bodies: wheel hubs, frame and decorative products
⑥Others: lower end covers of shock absorbers, compressor brackets, clutch pedals and brake pedals.
The figure below shows the summary and proportion of aluminum alloy die castings for automobiles. It can be seen from the figure that the die-cast aluminum alloy has been widely used in the automotive industry.
The future development trend of die-cast aluminum alloys
In recent years, the requirements of technical indicators such as power, safety, comfort and lightweight in the electric new energy automobile industry has continuously improved. The required aluminum alloy products are gradually developing in the direction of thin walls, high strength, low costs and integrated structure, which provides the application foundation and source power for the development of die casting technology. In recent years, the development of aluminum alloy die casting technology has generally been through continuous optimization and adjustment of the composition of alloy materials, combined with control and adjustment of high vacuum die casting technology and heat treatment process parameter to give full play to the process characteristics of alloy materials. With the help of high-pressure injection and low speed filling, the comprehensive mechanical properties of die casting alloy materials are continuously improved. With the continuous deepening of military and civilian integration, according to the integrated lightweight design of the structure, a large number of cylindrical projectiles can realize mass production by die casting process due to their low requirements for fatigue performance, which shortens the product development cycle, reduces the production cost and provides a development basis for the promotion and application of die-cast aluminum alloys.