1.2
Mechanical properties
The mechanical properties of squeeze casting samples are generally higher than those of metal mold casting, because the grains are significantly refined under the action of mechanical pressure. According to the Hall-Petch formula, the strength of the workpiece increases with the reduction of the grain size, that is, complete grain refinement. At the same time, the increase of grain boundaries and the distribution of eutectic Si and a small amount of strengthening phase Mg2Si also have a pinning effect on the dislocations in the α-Al matrix. In addition, casting defects greatly affect the elongation at the break of the alloy, and the applied pressure of squeeze casting can reduce the casting defects inside the
casting and increase the density of the casting structure; the macroscopic performance is the improvement of the strength of the sample.
When the α-Al matrix of face-centered cubic structure is subjected to a load perpendicular to the slip plane, the slip system will be activated. Slip rather than cleavage, and there is no cleavage fracture. The electron microscope photos of fracture morphology of castings with different casting methods were further photographed and observed. Figure 3 shows the tensile fracture morphology of PMC, LSC and SSC samples. It can be seen from Figure 3a that the morphology of eutectic Si is a long and narrow sheet at the grain boundary, which is prone to cracks and expands along the grain boundary. With the accumulation of stress, it is torn, leaving obvious tear edges, well-defined facets and river-like patterns due to disordered grain orientation, coarse sizes, and hindered extension of the crack at the grain boundary.
The fracture mode is a transition mode between brittle fracture and ductile fracture, which is a quasi-cleavage fracture biased towards brittle fracture. It can be seen from Figure 3b that the tearing edge in the tensile fracture is narrowed, and small and deep dimples are densely distributed. The fracture has no obvious layers, and no separation steps or facets are found. Therefore, it is judged that the fracture form has a tendency of ductile fracture. It can be seen from Figure 3c that the size of the dimples is slightly larger, the distribution is uniform, and the shape is round, which conforms to the characteristics of equiaxed dimples; at the same time, there are fewer tearing edges on the fracture, and the sample as a whole shows ductile fracture. It was found that the elongation of the samples was controlled by the size of the dendrites and the aspect ratio of the eutectic Si phase. Combined with the above, the elongation of the squeeze cast samples was improved compared with the metal mold casting. The eutectic Si phase of the SSC sample is refined, which reduces the crack source of the brittle phase. The large dimple size indicates that the micropores in the sample aggregate, and the crack propagation path increases. Macroscopically, the elongation rate increases significantly.
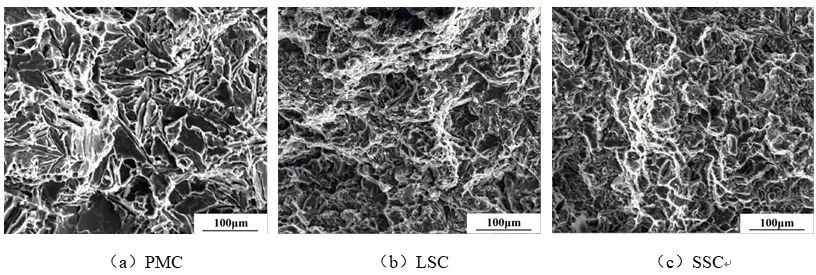
Figure 3 Tensile fracture morphologies of castings with different casting methods
2.
Conclusion
(1) The casting method significantly affects the microstructure of A356 aluminum alloys. The α-Al grains of the metal mold casting samples are coarse dendrites with an average size of 137.807μm, and the eutectic Si phase exists in the shape of laths and lamellae with an average diameter of 4.04μm. The grains are refined with the smallest cellular crystals and an average size of only 43.512μm. The eutectic Si phase changes into slender long rods, and the average diameter drops to 2.05μm. The average size of the grains obtained by semi-solid squeeze casting is 64.824μm, which is slightly larger than that of liquid extrusion casting, but the shape is more rounded. The average diameter of the eutectic Si phase drops to 1.61μm, which becomes a worm-like shape with small sizes, curved shapes and blunt edges.
(2) Vacancies and dislocations, grain boundaries and a solid solution of elements will cause the thermal conductivity of the alloy to be lower than that of pure metal, but the thermal conductivity of A356 aluminum alloys is the most sensitive to the morphology of the eutectic Si phase. With the decrease of eutectic Si phase sizes and aspect ratio and the increase of roundness, the thermal conductivity and thermal diffusivity tend to increase. The thermal conductivity of the metal mold casting is 150.064W/(m∙K), and the thermal conductivity of the liquid extrusion casting is increased to 2.0%, while the semi-solid extrusion casting has larger α-Al grains, round shapes, and small eutectic Si and passivation of the boundary; reduce the scattering probability of free electrons, and the thermal conductivity reaches 160.220 W/(m∙K), which is 6.7% higher than that of metal mold casting.
(3) Through squeeze casting, the internal casting defects of A356 aluminum alloys can be reduced and its mechanical properties can be improved. The tensile strength of the metal mold casting is 179.930MPa, the elongation is 3.19%, and the hardness (HB) is 55. The tensile strength of the liquid extrusion casting reaches 209.446MPa, the elongation is 6.93%, and the hardness (HB) increases to 64. The tensile strength of the semi-solid extrusion casting reaches 223.514MPa. The elongation is 13.68%, and the hardness (HB) is increased to 71, which is improved compared with the metal casting.