1.
Analyses
1.1
Thermal conductivity
The physical process of heat conduction of aluminum alloy
die-cast parts is mainly realized by the migration of free electrons. With a certain temperature gradient as the driving force, the electrons move directionally in the direction of decreasing the temperature gradient through continuous collisions and the energy was transferred from the high-temperature to the low-temperature area to complete the heat conduction. It is expressed by the Wiedemann-Franz law as follows:

(2)
That is, under non-low-temperature conditions, the ratio of the thermal conductivity (λ) of the metal to its electrical conductivity (σ) is approximately constant. Therefore, starting from the electrical conductivity, the thermal conductivity mechanism of the alloy was explored.
ρ=ρT+ρR (3)
The average distance of an electron travels between two collisions is called the mean free path.
Deduced from Bloch's theorem, the mean free path of electrons in aluminum alloys is limited by the degree of crystal structure integrity. When the temperature gradient is constant, the more complete the crystal structure of the aluminum alloy is, the longer the mean free path and the electrical conductivity become. The alloy resistance is specifically constituted by Matthiessen's law:
ρ=ρT+ρR (3)
In the formula, ρT is the basic resistance of the alloy, which is only related to temperatures. ρR is the impurity resistance, which is composed of
ρR=ρp+ρss+ρd+ρgb (4)
In the formula, ρp, ρss, ρd and ρgb are the resistances caused by precipitates, solid solubility, dislocations and grain boundaries to alloy atoms.
The degree of influence on electron motion mainly depends on the number and structure of displacement, grain boundaries, a solid solution of alloying elements and intergranular precipitation equal defects. The larger the dislocation density and grain boundary area are, the more scattered electrons and the lower the thermal conductivity of the alloy become. The higher the solid solubility of the elements in the alloy is, the more serious the lattice distortion of the matrix is caused. Destroy the order degree of atoms in the aluminum matrix and the distribution of the original periodic electric field, resulting in defects and stress fields. The more the number of intergranular precipitates, the larger the size and the greater the scattering effect on electrons become. The mean free path of electrons decreases, and the thermal conductivity of the alloy declines.
At room temperatures, the low density of vacancies and dislocations has little effect on the resistivity, and in the case of only changing the casting method without plastic deformation and annealing, there is no significant difference in the dislocation density between different samples. Therefore, the effect on thermal conductivity can be ignored. The change in the cooling rate will change the grain size of the Al matrix and the total area of the grain boundary to a certain extent. LI B and others also pointed out that the change of the grain size has little effect on the thermal conductivity, and the thermal conductivity does not decrease significantly with the significant refining of the grain size.
For the Al-Si alloy, Si and Al form a replacement solid solution, but the solid solubility of Si in Al is very small. The maximum saturated solid solubility is only 1.65%, and only 0.05% at room temperatures. The remaining Si in the elemental form will form an Al-Si eutectic structure with Al. The mass fraction of Si in the A356 aluminum alloy is about 7.06%, only a very small amount of which is dissolved in the Al matrix; more is precipitated in the form of Al-Si eutectic. The atomic radius of Si (0.134nm) is very close to Al (0.143nm), and the lattice distortion of the Al matrix caused by the solid solution of Si atoms is very small, so the solid solution of Si in the matrix has little effect on the thermal conductivity of Al. The main influence is eutectic Si precipitated at grain boundaries. Bin Li and others also believed that when the Si mass fraction was 7.0% to 12.8%, the lattice distortion of the Al matrix was very small, and the change with Si content was not obvious.
The splitting of the intergranular precipitation relative to the matrix is the main reason that the thermal conductivity of A356 aluminum alloy is lower than that of pure Al. According to the SEM pictures of the eutectic Si phase of the three casting methods, the schematic diagram of its hindering effect on electron migration is shown in Figure 1. The eutectic Si phase of the PMC sample has a large lath-like size and is concentrated and distributed, and it is difficult for electrons to pass through or bypass the eutectic Si grains to complete the energy transport. Under the action of mechanical extrusion force, the density of the alloy is increased and the atomic spacing is shortened. The matrix connectivity is enhanced, and the free electron free path is increased, which improves the thermal conductivity of the alloy. LSC inevitably increases the grain boundary area when refining the grains of the α-Al matrix, but at the same time, it also achieves a significant refining effect on the eutectic Si grains, making them into long rods. The area is greatly reduced, and the width is widened. The overall performance is the improvement of energy transport efficiency, that is, the increase of thermal conductivity; the intergranular eutectic Si phase of the SSC sample is broken and spheroidized to a certain extent. The edge becomes blunt, and the whole becomes worm-like.
The passivated eutectic phase edge can reduce the probability of scattering. The main mechanisms include reducing the scattering area, changing the scattering collision to cut through, increasing the free path of electrons in the matrix, and changing the scattering direction, as shown in Figure 2. The mechanism mainly includes reducing the scattering area, changing the scattering collision to cutting through, increasing the free path of electrons in the matrix and changing the scattering direction, as shown in Figure 2. It can be seen that the spheroidization of the eutectic Si phase will greatly reduce its hindering effect on free electron migration and improve the thermal conductivity of A356 aluminum alloys.

Figure 1 The schematic diagram of the principle of scattering of free electrons on the eutectic Si phase
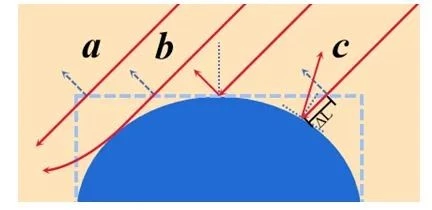
Figure 2 The effect of the grain boundary shape on electron scattering