2.
Knowledge communities with a holistic method
The team involved in this article includes materials science and casting technology scientists, wheel experts and machine builders, as shown in Figure 5. In this article, a system and process method developed can effectively solve the challenges posed by the above issues.
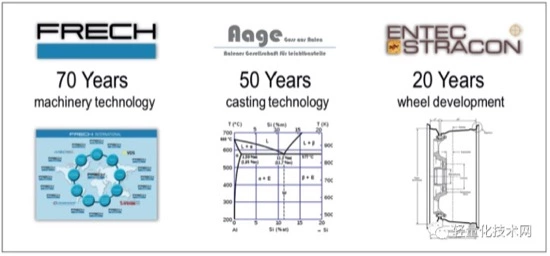
Figure 5 TURBU-PRESSURE-CASTING EXPERT COMMUNITY
This holistic method to specific requirements for products achieves a positive energy balance in the manufacturing process and promises to effectively meet the changing needs of the automotive industry. Furthermore, in this process method and manufacturing system, resource saving effectiveness is always considered.
All in all, the team of TURBU-PRESSURE-CASTING (no-turbulence pressure casting) technology experts combines active parts of existing technologies such as low-pressure casting or die casting in the mold. This makes it possible to make light metal wheels very efficiently and flexibly with the TURBU-PRESSURE-CASTING technology mentioned in this article, although the cross sections of wheel products vary greatly.
3.
The casting process and its advantages
There is no turbulence for TURBU-PRESSURE-CASTING (no turbulence pressure casting) introduced in this article, coupled with pressurized pouring and closely related to the mold temperature, so it can finally generate a near net shape target wheel geometry despite the high casting speed, which means that there is no need for extensive rework and subsequent processing, as shown in Figure 6.
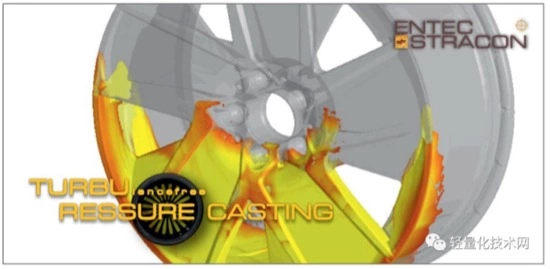
Figure 6 The overview of TURBU-PRESSURE-CASTING technology
The light alloy wheels produced by the patented TURBU-PRESSURE-CASTING (non-turbulent pressure casting) process already have the strength required by the wheels after casting, so there is no need for additional energy-intensive manufacturing processes, such as cutting, flow forming or heat treatment (T6), etc.
To comply with the CO2 emission limits, automotive cast
aluminum alloy wheels are increasingly being provided with expensive additional plastic covers. With the TURBU-PRESSURE-CASTING technology (no turbulence pressure casting), it is possible to produce an aerodynamically smooth wheel finish through the casting process, thus eliminating the need for plastic wheel covers. Furthermore, bolt holes or rigid structures can also be realized with this process, which can be done by standard methods with only a little machining or no machining at all.
4.
Barrier-free mold replacement in die-cast systems
The TURBU-PRESSURE-CASTING (Pressure Casting without Turbulence) team with partners has developed a casting unit based on a special cold chamber die-cast machine, which makes it possible to process aluminum alloy wheels immediately after the wheels have been casted, so that only good parts can leave the unit, and a small amount of finishing can be done in the center of the wheel. Therefore, there is no loss of value within the production chain, as shown in Figure 7.
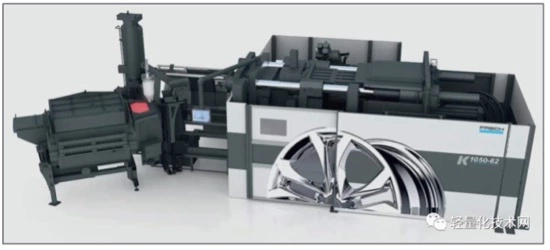
Figure 7 TURBU-PRESSURE-CASTING complete casting units
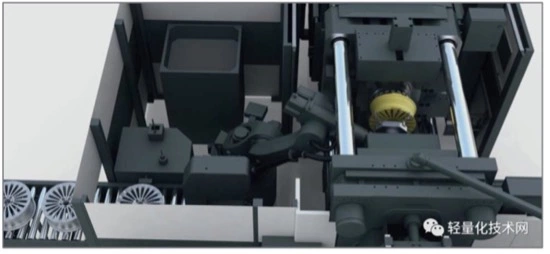
Figure 8 Process details in the TURBU-PRESSURE-CASTING casting unit
Furthermore, thanks to the high degree of automation of the entire system, the foundry cell meets requirements for all Industry 4.0-related quality and enables fully automatic mold changes in less than 10 minutes. With a cycle time of less than 2 minutes, the automated cell sets new standards in production speed, as shown in Figure 8.
Compared with the forging process, the advantage of low-pressure casting is that the molds are very cost-effective. Especially for low-volume wheel production, the price of low-pressure casting molds has a much lower impact on part prices than molds for forged wheels. This advantage is also integrated into the TURBU-PRESSURE-CASTING (turbulence-free pressure casting) casting unit, so the molds of TURBU-PRESSURE-CASTING (turbulence-free pressure casting) are much cheaper than traditional die-cast molds or forging molds, thanks to the schematic design of the split mold or fixture, as shown in Figure 9.
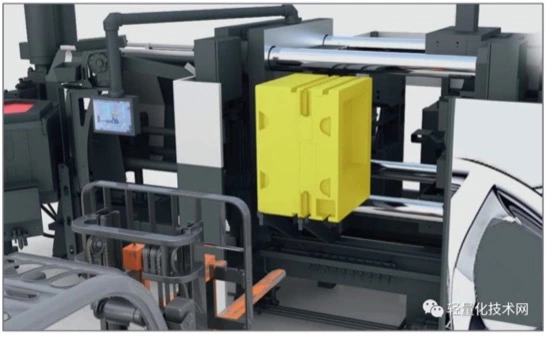
Figure 9 Changing fully automated molds
5.
The outlook for results and mass production
All in all, 80% of TURBU-PRESSURE-CASTING (non-turbulent flow pressure casting) casting unit is used for wheel production, and some other functions are for a better man-machine environment and environmental friendliness. The Turkish company CMS, which is part of the TURBU-PRESSURE-CASTING (no-turbulence pressure casting) team of experts, is a Tier one supplier for wheel manufacturing and is responsible for promoting the technology to the market. It is expected that the first batch of aluminum alloy wheels mass-produced using TURBU-PRESSURE-CASTING (no-turbulence pressure casting) technology will be available and introduced to the market by October 2019.