1.1
Calculation of meshing length between aluminum alloy bolts and magnesium alloy shells
In the threaded connection, the internal thread slippage caused by overload is not easy to find, and the maintenance cost of the internally threaded parts is high. Therefore, when designing the threaded connection, the failure of the joint overload should be a fracture of bolts rather than the pulling of internal threads. Under the condition of constant thread specification and material strength, the increase in thread engagement length can increase the shear cross-sectional area and the shear strength of internal and external threads. According to the "VDI 2230 System Calculation Specification for High-impact Bolted Connections", the calculation formula of the minimum engagement length meff is shown in Equation 3.
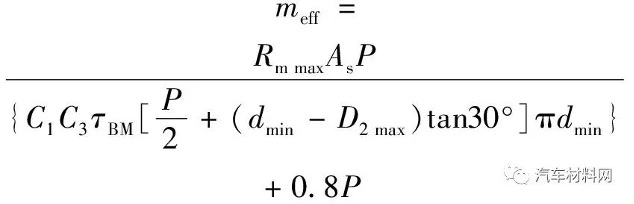
(3)
In the formula, Rm max is the maximum tensile strength of the bolt. As is the stress cross-sectional area of the external thread; P is the pitch; dmin is the minimum outer diameter of the external bolt; D2 max is the maximum pitch diameter of the internal thread; C1 and C3 are correction coefficients, generally adopting 1.000 and 0.897 for internal thread blind holes; τBM is the internal thread’s shear strength, which is 50% of the tensile strength. Taking the magnesium alloy shell material AZ91D, the aluminum alloy bolt material EN AW-6056 and the M8 thread of the flange surface bolt specification commonly used in the powertrain as an example, the calculated minimum thread engagement length meff is about 1.7 d (the nominal diameter of the thread, unit mm). For the steel bolts of grade 8.8 of the same specification, the engagement length needs to reach 2.7 d.
1.2
The selection of surface treatment of aluminum alloy bolts
Because the strength of the aluminum alloy is much lower than that of steel, to obtain the same assembly pre-tightening force as 8.8 steel bolts of the same specification, the tightening method of
aluminum alloy bolts must adopt the superelastic tightening. In engineering practice, superelastic tightening can be achieved by the torque-angle method. This assembly process can reduce the dispersion of bolt pre-tightening force. At the same time, aluminum alloy bolts require a stable friction coefficient. By reducing the difference in friction coefficient of mass-produced fasteners, the tightening torque and locking force under alternating loads can be stabilized. To stabilize the coefficient of friction, the most commonly used surface treatment of aluminum alloy bolts today uses water-based lubricants containing polymers. The lubricant is coated by dipping, and forms a lubricating film on the surface of the bolt after drying, which can ensure that the friction coefficient between the aluminum alloy bolt and the internal thread of the magnesium alloy shell is controlled within the range of 0.09 to 0.16. Because the composition of the sealing medium may damage the lubricating film, the influence of the sealing medium on the friction coefficient should also be considered when selecting the surface treatment. In practical applications, lubricants that are not sensitive to the sealing medium should be selected as much as possible, and the liquid sealing medium should be strictly controlled.
1.3
The torque-angle assembly process
The effectiveness of the above scheme can be verified by torque failure tests. As shown in Figure 4, technicians sequentially applied torque to the bolts of six samples until they failed, and recorded the torque rotation angle curve from the beginning of tightening to the yield of the bolts, and then to failure.
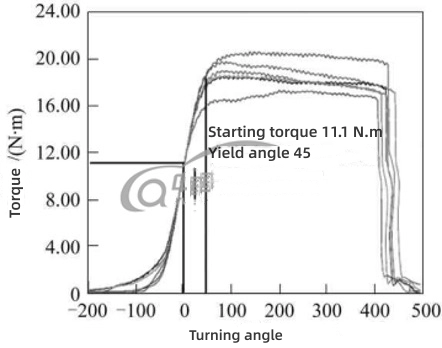
Figure 1 Torque rotation angle curve of sample bolts
The test results show that the failure of the 6 samples is the fracture of the bolt, which proves that the design of the engagement length meets the requirements. The yield torque of bolts is 15.66 to 19.07 N·m. The average yield torque is 17.96 N·m, and the yield torque dispersion is 7.1%. According to the range of commonly used tightening guns (generally 50.00 N.m), the initial torque is determined to be 11.00 N.m, and the yield angle is about 45°. Therefore, it can be determined that the tightening process of the aluminum bolt joint is the initial torque of 11.00 N.m. The yield angle is 45°. It has been confirmed that the bolt’s pretightening force also meets the design requirements under this process.
2.
Conclusion
Aluminum alloy bolts can fundamentally solve the problem of galvanic corrosion of the magnesium alloy shell of the new energy electric drive assembly. Some problems in the application of aluminum alloy bolts on the housing of the new energy electric drive assembly are studied, and came to the following conclusions.
(1) The meshing length of aluminum alloy bolts and magnesium alloy shells is 1.7 d, which can be reduced by 1.0 d compared with steel bolts of the same specification. The use of aluminum alloy bolts can make the structure of the connected parts more compact, and the corresponding material consumption is also reduced.
(2) The surface treatment of aluminum alloy is generally surface lubrication, and the influence of the sealing medium must also be considered when selecting the surface treatment.
(3) Through the failure test of the torque, it is verified that the meshing length of the aluminum alloy bolt meets the design requirements, and the process parameters of the torque rotation angle are determined at the same time.